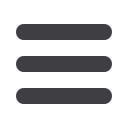
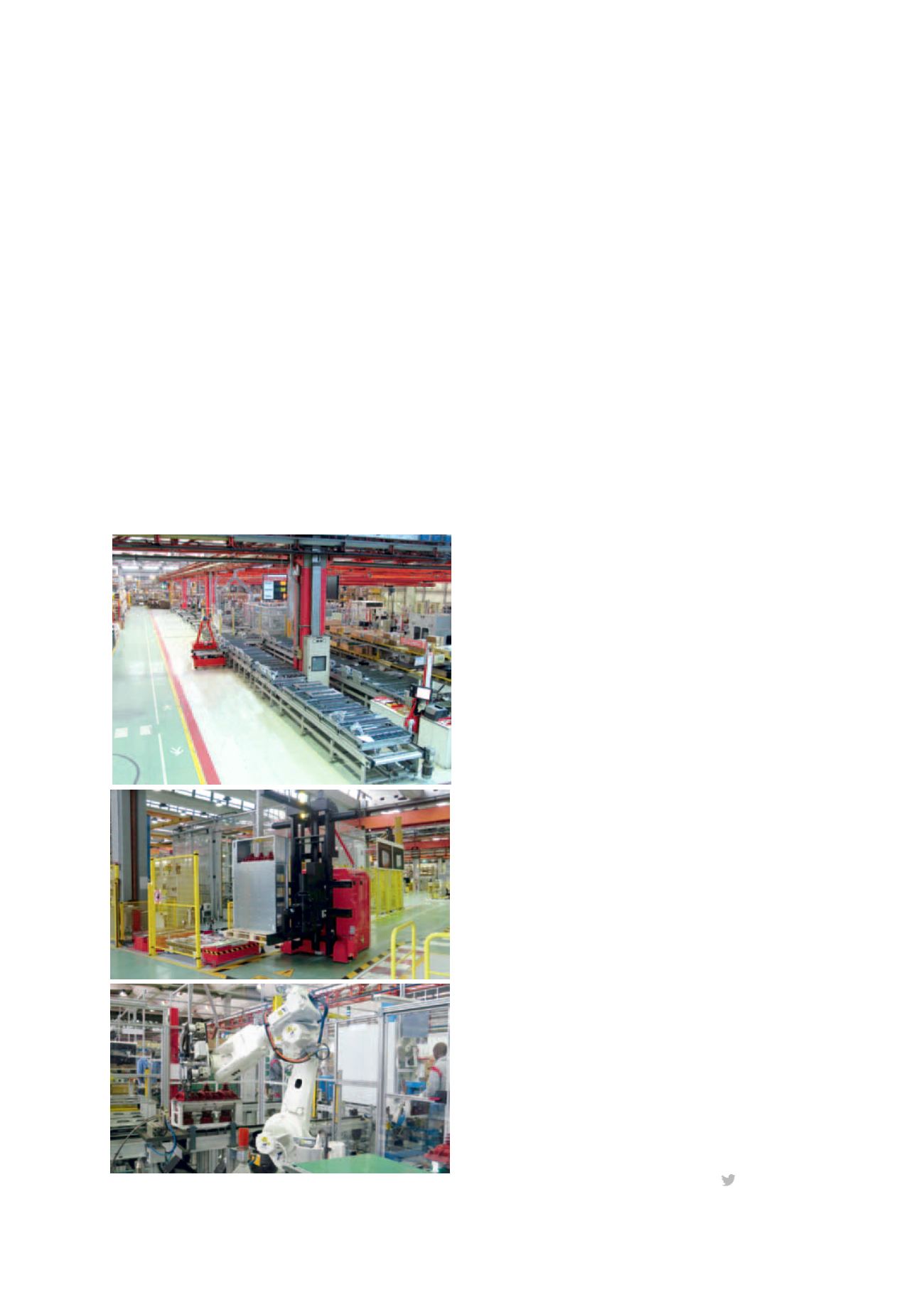
25
rmo
giugno/luglio 2017
con metodi organizzativi all’avanguardia ed estesa ca-
pacità di valutare i miglioramenti introdotti, sia la co-
noscenza sul comportamento e le modalità di guasto
dei componenti meccanici, garantita dai fornitori degli
stessi, sia le tecniche di fusione sensoriale, simulazione
del processo e in generale di data analytics che pos-
sono portare i partner di ricerca. “Il Lighthouse plant
ProMa è un laboratorio costruito su un impianto fles-
sibile e autonomo - conclude Fogliazza -, inserito in un
contesto produttivo all’avanguardia nell’integrazione
di tecnologie dell’informazione e dell’organizzazione.
Dal team di ricerca ci aspettiamo lo sviluppo di risultati
innovativi che consentano di fornire impianti sempre
più autonomi e flessibili, e nello specifico in grado di
inviare richieste sulla necessità di eseguire interventi di
manutenzione prima che si verifichino guasti, e di adat-
tare il proprio comportamento alle condizioni reali di
carico. Ci si aspetta quindi di ottenere una squadra di
persone formate su tecniche di analisi di grossi volumi di
dati, e nello sviluppo di algoritmi di apprendimento au-
tomatico, da iniettare negli uffici tecnici delle aziende
coinvolte nell’iniziativa”.
L’Industria 4.0 è qui.
MCM ha sviluppato strumenti
coerenti con la filosofia 4.0 sfruttando i sensori già
presenti nei propri impianti e integrandone altri. L’a-
zienda ha quindi adeguato l’architettura complessiva
di controllo, che già da tempo prevede nodi per l’ela-
borazione dell’informazione generata e richiesta dai si-
stemi di produzione. “Siamo riusciti a creare una serie di
strumenti di verifica continua dello stato dell’impianto -
spiega Fogliazza - in termini di affidabilità, sostenibilità,
qualità e precisione, con output specifici per operatori,
pianificatori della produzione, manutentori, fornitori
di servizi e costruttori di macchine”. Al fine di creare
sistemi di produzione flessibili e autonomi, e cogliere
le opportunità sottese alla logica di connettere le mac-
chine, l’azienda ha quindi saputo fondere più contri-
buti trasversali, per gestire al meglio la mole di dati che
si raccolgono: meccanica di precisione, automazione,
controllo e supervisione. A questi si aggiungono com-
petenze in tecnologie ICT e la capacità di impiegarle in
modo innovativo, grazie a un know-how accumulato in
oltre 30 anni di produzione di FMS e centri di lavoro do-
tati di un sistema dedicato all’elaborazione delle infor-
mazioni richieste e generate dal mezzo di produzione.
La digitalizzazione è al centro della strategia Next Level
del Gruppo ABB, applicata non solo nell’implementare
tecnologie digitali per ottimizzare processi produttivi
interni, ma anche nello sviluppo di prodotti, sistemi,
software e servizi avanzati per i clienti. Caratteristica
distintiva di ABB è pertanto la capacità di testare quelle
stesse soluzioni digitali industriali che l’azienda propone
al mercato nel portafoglio ABB Ability, prodotti e so-
luzioni Industria 4.0 a loro volta progettati, sviluppati
e realizzati in realtà produttive all’avanguardia, basate
su concetti di automazione, integrazione e dinamicità.
“Il nostro stabilimento ABB di Dalmine - dice Golinelli
- insieme alle sedi di Frosinone e Santa Palomba, è uno
dei siti produttivi più avanzati. Gli investimenti di ABB
in Italia hanno fatto e fanno delle fabbriche italiane del
Gruppo una best practice a livello internazionale, rico-
nosciute come Centri di eccellenza per lo smart manu-
facturing e trasformatesi naturalmente in dimostratori
reali delle applicazioni digitali legate a Industria 4.0”.
@marcocyn
Nelle tre immagini, degli esempi di impianti faro realizzati da ABB.