
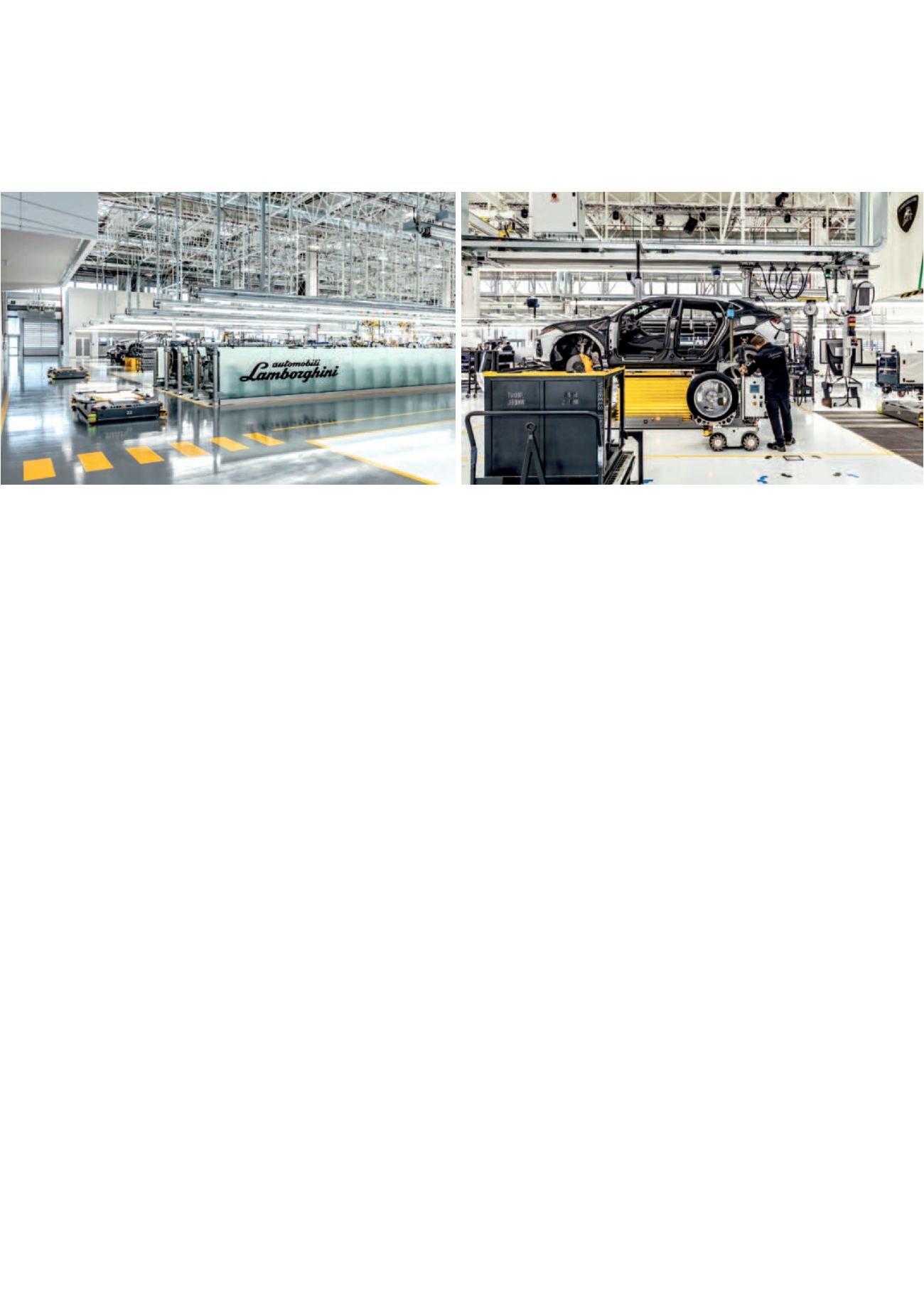
60
rmo
aprile 2018
Il secondo cardine del processo produttivo va sotto
l’acronimo di MES, ossia Manufacturing execution
system. Si tratta del grande software che regola, re-
gistra e monitora tutto: come si spostano i carrelli,
quali operazioni sono state effettuate e da chi, che
viti si possono usare con un determinato avvitatore,
con quanta pressione e così via.
Il terzo sono i robot, che per la verità qui si dovreb-
bero chiamare ‘cobot’ o robot collaborativi. Non ci
sono gabbie entro cui sono confinati, ma stanno
gomito a gomito con i lavoratori. Non sono moltis-
simi e ce ne sono di almeno tre tipi: uno che stende
il silicone sul parabrezza, prima che gli operai lo
applichino con una manovra e degli aggiustamenti
che ancora si preferisce affidare agli uomini. Uno
che, muovendosi su un ulteriore carrellino, avvita
la parte posteriore della carrozzeria al telaio, con
una soluzione finora unica in Europa. E un terzo
che prende gli pneumatici da uno scaffale e li pre-
dispone per il montaggio sull’auto, evitando che il
peso ricada sui lavoratori.
Il ‘cervello’ al centro di tutto.
Il vero ‘compagno’
dei lavoratori è però un touchscreen a cui gli opera-
tori si devono rapportare in tutti i loro passaggi. Ci
si ‘logga’ passando un braccialetto (o un ‘ciondolo’)
che identifica ogni lavoratore. Al touchscreen si co-
munica ogni lavorazione, si riceve la conferma che
l’operazione è stata fatta correttamente, si segna-
lano eventuali problemi o si chiedono lumi sulle tec-
niche più adatte per le lavorazioni meno frequenti,
quelle richieste dall’estrema possibilità di perso-
nalizzazione che la fabbrica permette. “Una volta,
per segnare i vari passaggi produttivi si doveva re-
gistrare tutto a mano, c’era un mare di carta. Ora
è tutto a video e soprattutto tutti i manuali sono
costantemente aggiornati”, spiega Niccoli.
A mano a mano che si avanza si ha l’impressione
di un impianto semplice, quasi banale nella sua as-
senza di quadri, attrezzi, fili. Niente di più falso:
la complessità è semplicemente gestita dalle solu-
zioni tecnologiche. A dominare sono i sensori, altra
tecnologia abilitante dell’Industria 4.0. Sono questi
che permettono di passare dalla ventina di avvita-
tori precedentemente richiesti in alcune stazioni a
uno solo, peraltro wireless. Il sistema riconosce le
bussole e le viti e rende possibile solo gli accop-
piamenti compatibili. Ogni auto conta circa 50mila
componenti e 105 centraline che dialogano tra
loro. Poco prima del ‘marriage’, ossia dell’incontro
tra la carrozzeria e il ‘power train’, un colpo d’oc-
chio al motore e agli assi a esso collegati toglie ogni
dubbio sulla complessità del processo.
Nel caso del SUV Urus c’è anche un altro elemento
di complessità che viene trasformata in gioco per il
guidatore: la possibilità di cambiare, agendo su una
sola levetta, sei differenti assetti: si va dalla varia-
bile da casa-e-ufficio a quella da corsa, fino a quelle
più esotiche: ‘terra’, ‘neve’ e ‘sabbia’. Quest’ultima
permette di portare l’auto addirittura sulle dune
del deserto, con una evidente strizzata d’occhio al
mercato degli Emirati Arabi. Agendo sulle leve cam-
biano l’altezza da terra, l’assetto delle sospensioni,
la potenza del motore. La quale è più simile a una
super-car che a tutti gli altri SUV in commercio (in
attesa di quello della Ferrari, che per ora è però solo
un progetto): il motore è un V8 biturbo da 4,0 litri
da 650 CV e 850 Nm di coppia. L’accelerazione da 0
A sinistra, i carrelli AGV che servono a spostare le auto da una stazione all’altra. A destra, un ‘cobot’, su carrellino, porta una ruota al montaggio.
FOCUS
AUTOMOTIVE