
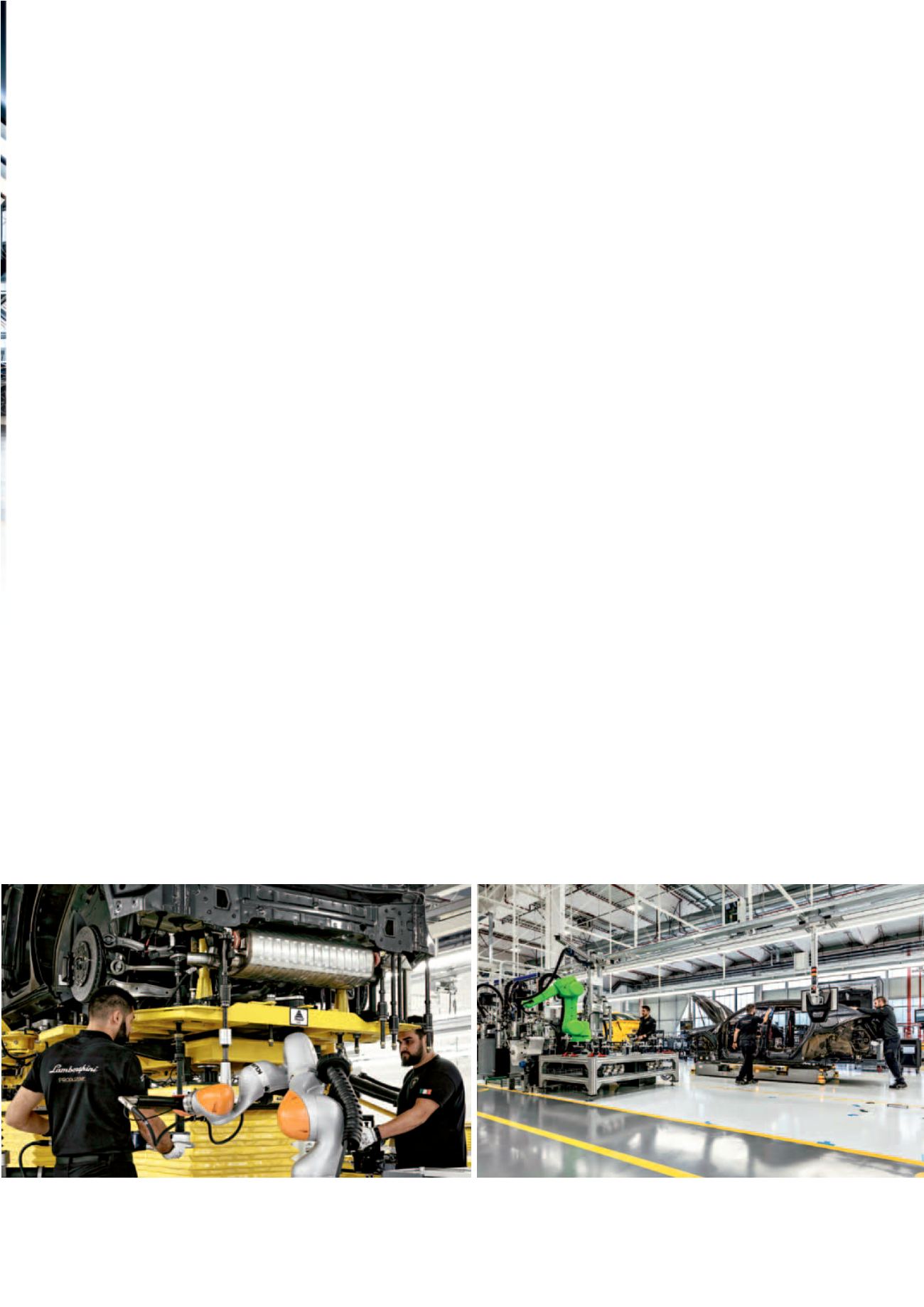
59
rmo
aprile 2018
pelle tagliata, cucita e sellata (cioè incollata sui
supporti) a mano da veri artigiani dentro la fab-
brica, come quelli che stendono la fibra di carbo-
nio sulla scocca.
Sono i due modelli che si ritrovano di più nel par-
cheggio. Ce n’è però anche un terzo, molto diverso.
È un SUV, chiamato Urus (il nome richiama quello
di un grande bovino estinto e richiama il toro, sim-
bolo della società). Negli ultimi due anni ha fatto
molto parlare di sé per vari motivi. Soprattutto per-
ché è stato il primo esperimento volto a creare un
ibrido tra una supercar e uno ‘sport utility vehicle’,
anche se alla Lamborghini ricordano orgogliosi il
fuoristrada LM 002 degli anni Ottanta, consideran-
dolo l’antesignano di tutti i SUV successivi.
Burocrazia al minimo.
Per crearlo - e per realiz-
zarlo in Italia - è stato messo in atto uno sforzo
da parte delle istituzioni, nazionali e locali, molto
impegnativo. Si calcola che siano stati impiegati
circa 80 milioni di euro pubblici, a fronte di un in-
vestimento privato nella fabbrica che nell’arco di
10 anni sarà di oltre un miliardo di euro. Questo
impegno, che è stato definito un esempio di nuova
politica industriale, è servito per evitare che la pro-
duzione avvenisse in un sito produttivo slovacco del
gruppo Audi, che dal 1998 è proprietario della Casa
al confine tra Modena e Bologna.
Ranieri Niccoli, chief manufacturing officer di Au-
tomobili Lamborghini, spiega che, pur essendo lo
stabilimento un esempio di Industria 4.0, molti qui
preferiscono la dicitura ‘Manifattura Lamborghini’,
a rimarcare il carattere di una fabbrica dove di pari
passo vanno le applicazioni tecnologiche più all’a-
vanguardia e l’artigianalità che ha sempre contrad-
distinto il marchio.
Percorrendo gli 80.000 m
2
della nuova fabbrica
(inaugurata nel dicembre scorso), quello che colpi-
sce non è tanto il colore bianco, l’assenza di rumori
assordanti e l’ordine, quanto piuttosto il fatto che
qui una vera linea produttiva non c’è. Ci sono delle
intelaiature bianche, in metallo, che tengono tutto
sospeso; tutto cala dall’alto, tramite enormi ‘pinze’
gialle che sollevano i telai delle auto ai grandi ser-
batoi da dove vengono iniettati i fluidi all’interno
dei modelli.
Gli elementi di innovazione.
A terra non ci sono
binari né rulliere. Ci sono invece alcuni dei prota-
gonisti della nuova fabbrica: i carrelli AGV (Auto-
mated guided vehicle), che spostano le auto da una
stazione all’altra. Lo fanno con una precisione mil-
limetrica (anzi con un margine di errore inferiore al
millimetro) grazie a un triplice sistema di guida, GPS,
laser ed elettromagnetica. Non è solo un modo per
rendere più semplici gli spostamenti. È quello che
permette di passare dal montaggio sequenziale al
montaggio modulare: ogni stazione ha la sua vita e,
se si rendesse necessario aggiungere o togliere dei
passaggi, lo si potrebbe fare con pochissimo sforzo,
senza ridisegnare tutto l’impianto. La parola d’or-
dine è ‘flessibilità’: ogni modello può essere per-
sonalizzato nei modi più curiosi (mentre visitiamo
l’impianto notiamo degli interni in pelle color verde
evidenziatore), senza che questo comporti l’ammon-
tare di tempo precedentemente richiesto. “Custo-
mer is king”, dice Niccoli. La prima casella nella lista
dei cardini dell’Industria 4.0 si può spuntare.
Nello stabilimento Lamborghini vanno di pari passo le applicazioni tecnologiche più all’avanguardia e la professionalità degli addetti.