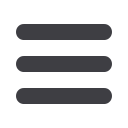
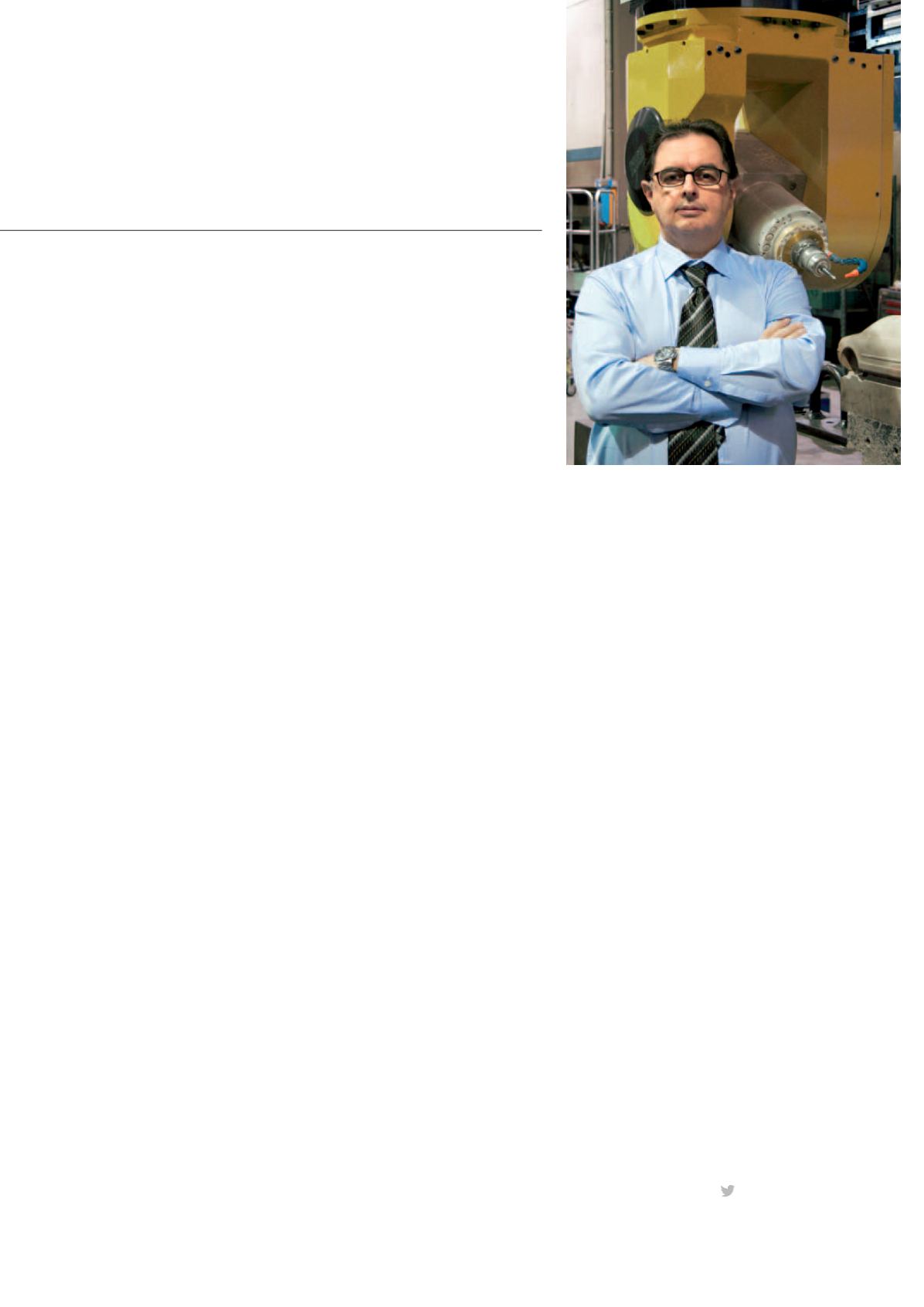
33
rmo
settembre 2016
di spessore nelle lavorazioni di foratura e svasatura di pacchetti di
materiali: carbonio, alluminio, titanio in varie sequenze. Tali cicli speciali
sono integrati con sistema di riconoscimento automatico in-process
del punto di cambio di materiali e contemporaneamente di verifica
dell’usura-rottura dell’utensile”.
Quali sono le opportunità per i costruttori di macchine utensili oggi?
“Il mondo industriale italiano - dice Dordoni -, dal mio punto di
osservazione, sta vivendo un momento positivo. Abbiamo buoni tecnici
con competenze elevate, un costo della manodopera estremamente
competitivo rispetto a Francia e Germania, il fenomeno del reshoring
(rientro in patria di alcune attività manifatturiere - ndr) è iniziato ormai
da qualche anno. Con queste convenienze i costruttori italiani possono
conquistare mercati importanti; dall’automotive all’aerospace, fino
alla lavorazione di geometrie complesse in genere come stampi e
meccanica generale”. E conclude: “Ci sono delle opportunità concrete
da cogliere, opportunità che dovrebbero coinvolgere anche le aziende utilizzatrici. Gli imprenditori, per far
sì che la propria impresa rimanga competitiva, dovrebbero pianificare un ricambio dei sistemi produttivi con
cadenze programmate. Come del resto succede in Germania. Il ciclo di vita di una macchina utensile non
dovrebbe superare i dieci anni di utilizzo, pena la perdita di produttività, efficienza e valore della stessa. Il
dato Ucimu è impietoso: l’età media del parco macchine utensili impiegato nelle aziende italiane non è mai
stata così alta negli ultimi 40 anni. Dobbiamo pensare a un nuovo modo di produrre. Ecco allora l’interesse
alla fabbrica 4.0. Siamo solo all’inizio di un percorso davvero innovativo. Ma questo progetto, nato in
Germania, deve essere adattato alla realtà italiana, alle medie e piccole aziende. Il primo passo è quello di
offrire loro tecnologie semplici, facili da integrare”. Cosa dire, innovare è d’obbligo.
ma riduce anche le vibrazioni al mandrino nelle mac-
chine utensili, migliorando rendimento e precisione.
Altri temi di ricerca sono le macchine ibride. Si tratta
di un progetto sperimentale tra Jobs e il Politecnico
di Milano per la costruzione di una macchina ad
asportazione di truciolo che, contemporaneamente,
è in grado di abbinare la tecnologia additiva 3D, di
polveri di metallo. Infine, ma non per questo meno
importante, la crio-tecnologia. Essa dovrebbe evi-
tare l’utilizzo dei lubrorefrigeranti nelle macchine
utensili. Il raffreddamento dell’utensile/pezzo è de-
mandato a un flusso di azoto liquido a -200 °C. Que-
sto tipo di refrigerazione è adatto per la lavorazione
del titanio e vari tipi di acciai.
Macchine evolute.
In occasione dell’Open House,
Jobs ha presentato ai visitatori alcuni modelli di mac-
chine utensili. Si tratta di sistemi adatti alla moderna
industria manifatturiera, in particolare per stampi e
modelli, aerospace e meccanica generale. Jobs, con
la sua produzione, riesce a soddisfare le esigenze
degli utenti. Si tratta di utilizzatori internazionali e
nazionali che hanno saputo reagire alla crisi e hanno
investito in nuovi prodotti, nuove macchine e nuovi
mercati. Ecco allora le macchine utensili dedicate al
settore aeronautico targate Jobs: tre eVer7, facenti
parte di due FMS che includono in totale dodici Jobs
eVer7 e una Jobs LinX concatenate con sistema di pa-
lettizzazione integrato, destinate alla lavorazione di
pezzi aeronautici in alluminio particolarmente com-
plessi e precisi; RoboDrim 200, un concetto nuovo di
macchina a montante mobile con un sistema di ge-
stione e sensorizzazione robotizzato presentato in
versione per l’esecuzione di lavorazioni di pre-assem-
blaggio di ali.
Per il settore automotive, invece, è stata messa sotto i
riflettori Laser Speeder, l’ultima realizzazione di Jobs
per il settore degli stampi di grandi dimensioni. Que-
sto sistema è equipaggiato con un’innovativa testa
laser per svolgere le operazioni di cladding, harde-
ning e measuring. Sarà integrata in un sistema fles-
sibile che comprende macchine fresatrici Jobs eVer7
insieme ad altre macchine per la lavorazione di grandi
stampi. L’impianto è equipaggiato con un sistema di
pallettizzazione.
Sempre per il comparto stampi, Frazer è un impianto
realizzato per un’azienda che opera nella subfornitura
nel settore della lavorazione di grandi stampi di imbu-
titura. La macchina è equipaggiata con tutti i software
e gli accessori necessari per consentire il funziona-
mento senza il presidio dell’operatore. Segnaliamo in-
fine Sigma Compact, il centro di lavoro verticale per la
lavorazione di stampi e meccanica generale.
@gapeloso