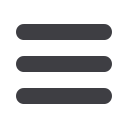
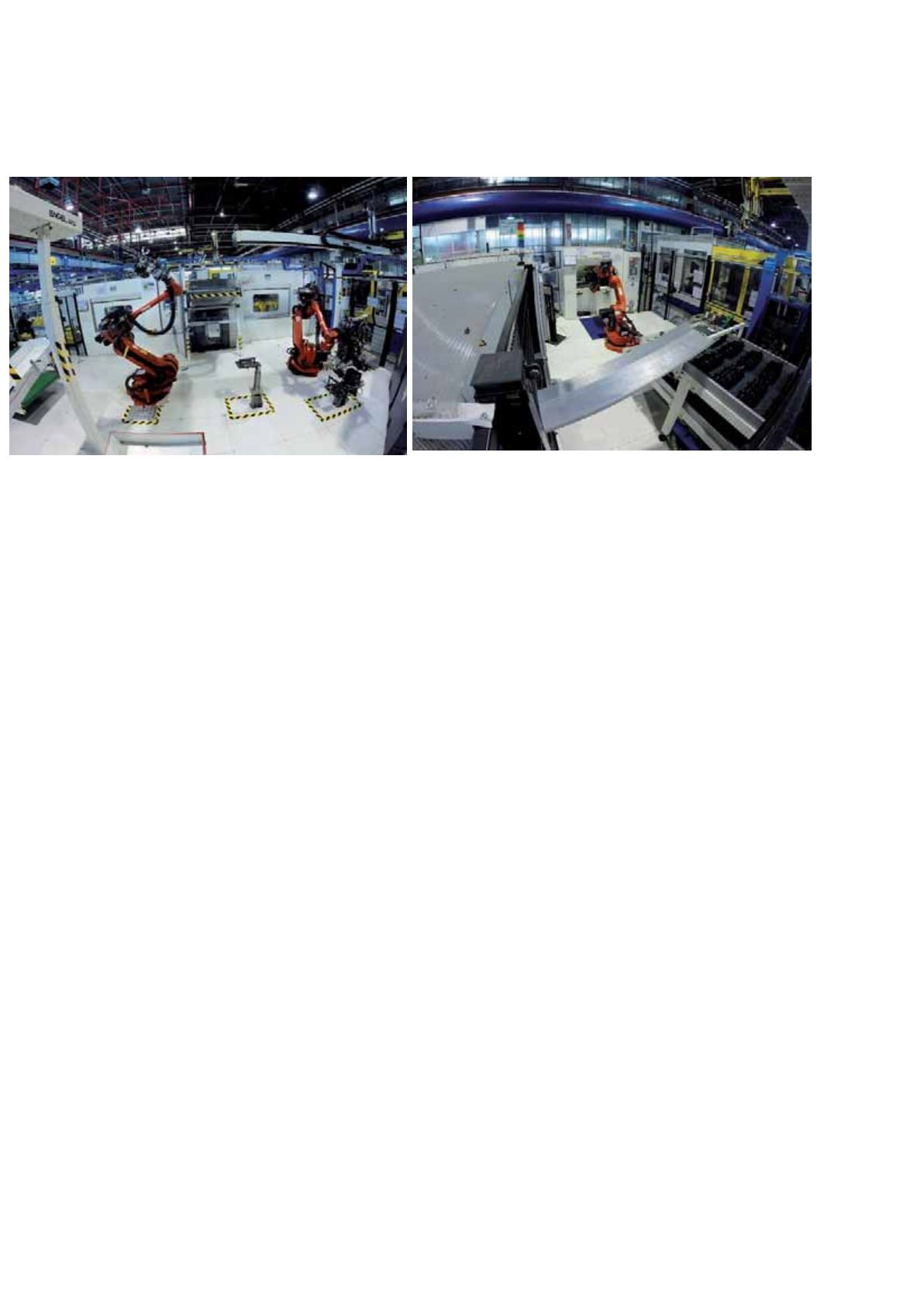
rmo
maggio2015
63
lizzati conduttori aria per auto a benzina, gpl, diesel.
«Partiamo dalla miscela dei granuli - spiega Marco Ca-
labrese - e arriviamo al prodotto finito che viene conse-
gnato direttamente nelle linee di creazione dei motori”.
In questo reparto le celle sono di due tipi: due sono
mono-robot, mentre altre due possono contare su due
robot per un totale, come detto, di sei robot Comau. In
questo reparto sono impiegati i robot Comau Smart NJ
25 e Smart NJ 45. L’automazione prevede in entrambi
i casi la presa del pezzo da un robot cartesiano e il de-
posito in una macchina che effettua un processo di
saldatura automatica. La differenza tra le due celle è
il numero di saldatrici - e di saldature - che vengono
utilizzate/effettuate. Il pezzo saldato viene poi posizio-
nato su nastro. L’automazione prevede anche la segre-
gazione e la storicizzazione automatica degli scarti e il
posizionamento dei pezzi per la fase di audit e controllo
in un’apposita nicchia.
Una collaborazione proficua.
I risultati ottenuti con
la robotizzazione sono positivi. Sia per livello di per-
formance e di obiettivi raggiunti, sia per la qualità
del rapporto con Comau. Se da un lato, infatti, preci-
sione, ripetitività e qualità attese sono state raggiunte,
dall’altro “il rapporto con Comau funziona anche per
altri ordini di motivi. Ad esempio a livello progettuale
e realizzativo: l’integrazione tra il robot cartesiano e gli
antropomorfi nelle linee del reparto plastica l’abbiamo
fatta assieme, sfruttando le competenze reciproche.
Inoltre Comau ci ha fornito anche gli organi di presa
per le celle e aggiungo, infine, una nota importante.
Sul lato software la proposta dell’azienda di Torino è
davvero ottima: i punti delle traiettorie sono facili da
programmare e spesso sono direttamente gli operatori
di linea o i manutentori che possono intervenire. Que-
sto non accade con altri produttori di robot”, spiega
Calabrese.
Il panorama è di dodici robot applicati complessiva-
mente per un totale di dieci celle e altri ancora in
arrivo. “Nel 2015 modificheremo la produzione di
collettori nella plastica e necessiteremo di altre linee
robotizzate nel reparto alluminio - dice il responsa-
bile - Comau è in prima fila per queste forniture visti i
risultati molto soddisfacenti che abbiamo ottenuto”.
L’incremento di qualità, produttività, ripetitività, resa
ed efficienza non è stato sinonimo, come dichiarato
da Calabrese in apertura, di riduzione del personale.
Al contrario anche in Magneti Marelli il lavoro dell’o-
peratore è evoluto ed è andato verso una maggior
specializzazione. “Il grande cambiamento per il tipo
di lavoro svolto dalle donne e dagli uomini che lavo-
rano da noi – prosegue Calabrese - è che si è ridotta
la pesantezza e la fatica delle mansioni e contempo-
raneamente è aumentato il livello di professionaliz-
zazione, di capacità tecniche necessarie per condurre
impianti automatizzati”.
L’automazione non ha, dunque, tolto posti di lavoro,
ma ha portato a una conversione delle competenze
richieste e a un aumento del personale legato all’au-
mento della produttività e della competitività di
un’azienda che ha visto ridurre i costi e aumentare
la qualità dei prodotti realizzati. “I risultati raggiunti
li abbiamo ottenuti anche applicando il WCM (World
Class Manufacturing) - conclude Calabrese - lo stan-
dard di produzione di tutte le aziende parte di FCA.
Attraverso l’automazione e una gestione del lavoro,
dei processi, degli approvvigionamenti, della sicurezza
al massimo livello, otteniamo i risultati descritti”.
Nell’impianto Magneti Marelli a Crevalcore operano dodici robot Comau, di cui sei nel reparto di produzione dei componenti in plastica.