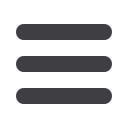
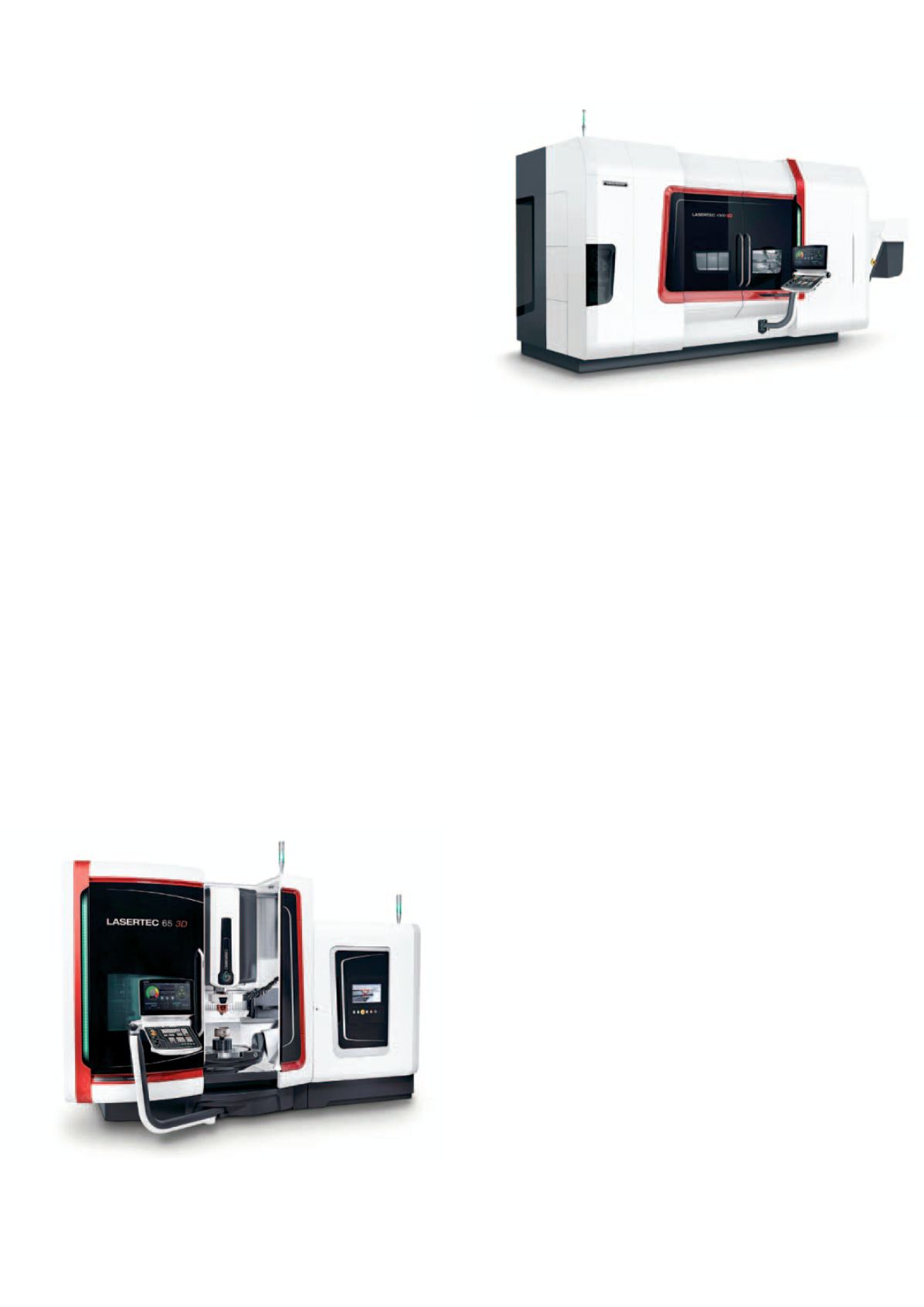
67
rmo
giugno/luglio 2017
utilizza il processo di riporto di materiale, applicato
mediante un iniettore di polveri metalliche, che con-
sente la lavorazione completa in assenza di camera di
processo e che con lotto di produzione uno vanta ve-
locità fino a dieci volte superiori alla produzione me-
diante letto di polvere. Tutto ciò in estremo accordo
con il trend che vede protagonista una produzione
sempre più personalizzata.
In aggiunta, i pezzi prodotti diventano sempre più
complessi. Sulla Lasertec 65 3D e sulla Lasertec 4300
3D è possibile realizzare profili a sbalzo senza geome-
tria di supporto e la seconda, in quanto macchina di
tornitura/fresatura, consente persino la lavorazione
completa su sei lati di componenti 3D. Il connubio
della sinterizzazione laser con riporto di materiale
e della lavorazione con asportazione di truciolo su
un’unica macchina apre orizzonti completamente
nuovi in quanto a applicazioni e geometrie realizza-
bili. Questa soluzione ibrida permette, in particolar
modo, una produzione di pezzi di grandi dimensioni
a costi ridotti. La flessibilità di passare dalla lavora-
zione laser alla fresatura consente, inoltre, di operare
in modo diretto su segmenti successivamente non più
raggiungibili a pezzo finito.
Nel caso della Lasertec 65 3D, DMG Mori ha compiuto
un ulteriore passo in avanti, offrendo anche la lavora-
zione di rettifica Ultrasonic in opzione. Questa soluzione
consente la produzione generativa di componenti in in-
conel, quali ad esempio le lame di una testa portapunta,
e la loro successiva lavorazione di finitura nella qualità
richiesta. È sufficiente applicare l’utensile di rettifica
Ultrasonic nel mandrino standard mediante un cambio
utensile automatico e il gioco è fatto. Grazie alla combi-
nazione tecnologica, DMGMori è riuscita a ottenere un
incremento della produttività di una o due volte. Infine,
si evita da un lato il processo di erosione e dall’altro si
allunga notevolmente la vita utile dell’utensile dovuto
alle forze di processo ridotte.
Con Lasertec 65 3D, DMG Mori ha integrato il processo di produzio-
ne laser generativo in una fresatrice a 5 assi.
Risparmio energetico.
Inoltre, Lasertec 30 SLM as-
sicura una lavorazione efficiente e redditizia grazie
al basso consumo di argon, pari a soli 70 l/h, e all’im-
pianto integrato di trattamento delle polveri, che
consente un processo di gestione polveri ottimizzato
e riduce al minimo la generazione di polveri sottili.
Il cambio delle polveri, inoltre, avviene in meno di
due ore grazie al modulo polveri intercambiabile. La
lavorazione sulla Lasertec 30 SLM è supportato da
una soluzione software completa, dotata di inter-
faccia utente standard del file CAD (RDesigner), che
include anche la gestione dei processi (ROperator).
A completamento ottimale del processo produttivo
abbinato alla tecnologia SLM, DMG Mori consente
la rilavorazione sui suoi centri di lavoro a elevata di-
namica, di cui è dotato il portafoglio di prodotti del
Gruppo. Sulle macchine HSC ad alte prestazioni o nel
caso degli advanced material come l’inconel anche sui
modelli Ultrasonic è, dunque, possibile raggiungere
i massimi risultati di precisione e di qualità delle su-
perfici.
Pezzi finiti di qualità.
Con Lasertec 65 3D, DMG Mori
ha integrato il processo di produzione laser generativo
in una fresatrice a 5 assi. La Lasertec 4300 3D combina
anch’essa il processo di produzione laser generativo
con la tecnologia di tornitura/fresatura in una zona
lavoro particolarmente generosa, pari a ø 660 x 1.500
mm. Questa soluzione ibrida intelligente riunisce la
flessibilità della produzione additiva con la precisione
della lavorazione ad asportazione di truciolo, consen-
tendo di realizzare pezzi completi nella stessa qualità
dei finiti. Il processo di produzione laser generativo
Lasertec 4300 3D, in quanto macchina di tornitura/fresatura, con-
sente la lavorazione completa su sei lati di componenti 3D.