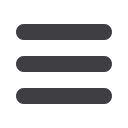
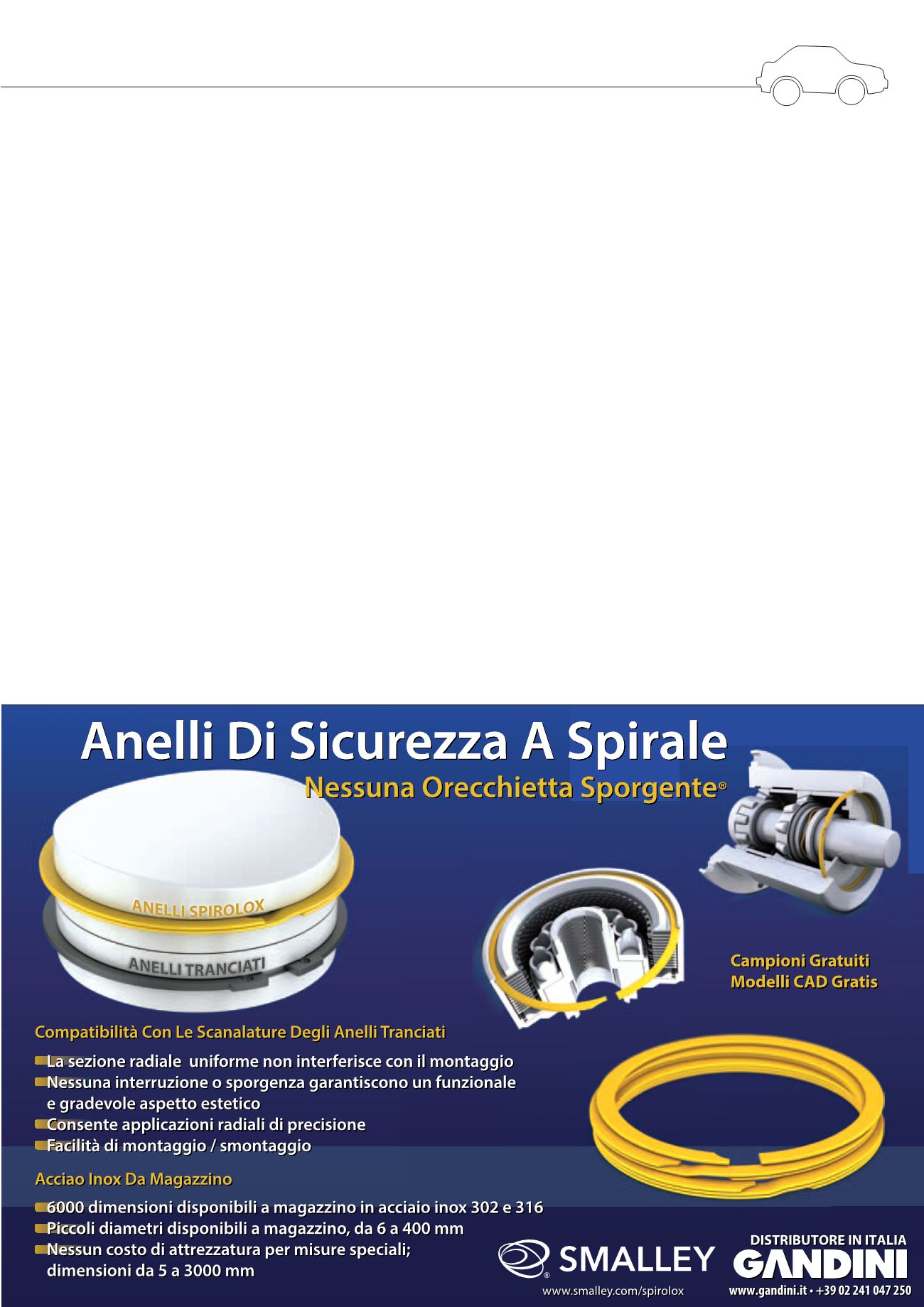
DOSSIER
INDUSTRIA AUTOMOTIVE
progettare 399 GIUGNO / LUGLIO 2016altoparlanti e interruttori, nonché l’iso-
lamento termico e acustico; il tutto in
una parete molto sottile.Tutto questo,
unitamente alla necessità di garantire
le tolleranze perfette che si addicono
a un’automobile di fascia esclusiva,
ha implicato un’imprescindibile ridu-
zione nell’impiego dei materiali più
pesanti per far sì che il panello potesse
essere sollevato senza compromette-
re la struttura complessiva.
Arpro è un materiale ben noto ai
tecnici di BMW, che l’avevano già
utilizzato inmolte applicazioni, incluse
quelle dei sedili dei modelli X5 e X6
e dello schienale della serie 5. La sua
capacità di essere stampato in forme
personalizzabili e di integrare cavi e
interruttori ha consentito la creazione
di una soluzione ad hoc per il modello
i8 che ne riducesse il peso del 22%
circa e ne migliorasse le prestazioni
in caso di impatto.
I vantaggi dei materiali alternativi
Un’altra ragione per prendere in con-
siderazione materiali alternativi è la
progressiva comparsa dei veicoli e-
lettrici che rappresentano un’ovvia
possibilità se si considera la neces-
sità di ridurre il peso il più possibile
per estendere la vita della batteria.
Anche se qualsiasi autovettura può
impiegare materiali leggeri, essi so-
no particolarmente importanti per i
veicoli elettrici, elettrici ibridi ed elet-
trici ibridi plug-in. L’uso di materiali
leggeri in questa tipologia di veicoli
può bilanciare il peso dei sistemi di
alimentazione, come ad esempio bat-
terie e motori elettrici, migliorandone
l’efficienza e aumentando l’autono-
mia in elettrico. In alternativa, l’im-
piego di materiali leggeri potrebbe
richiedere l’uso di una batteria più
piccola ed economica, mantenendo
però costante l’autonomia in elettrico
dei veicoli plug-in.
Lo sviluppo dei veicoli elettrici è anche
una risposta alla forte pressione cui è
sottoposto il settore automobilistico
in materia di emissioni, caratterizzata
dalla necessità di adempiere in tempi
brevi a obiettivi inderogabili, decisivi
e complessi. Entro il 2020 e il 2025
le OEM europee devono ridurre le
emissioni medie di CO allo scarico
al di sotto di 95 g di CO
2
/km e poi di
75 g di CO
2
/km. Pertanto, i produttori
sono chiamati ad affrontare una sfida
decisiva e un eventuale fallimento nel
raggiungimento di questi obiettivi po-
trebbe risultare catastrofico compor-
tando severe sanzioni su ogni singola
vettura non conforme prodotta. La
soluzione per adeguarsi alle nuove
norme è quella di utilizzare materiali
leggeri innovativi all’interno del telaio
della vettura, ma la vera sfida è quella
di convincere i designer, i produttori
e i compratori di autovetture del fatto
che questimateriali sono realmente in
grado di garantire i necessari livelli di
resistenza, stabilità e sicurezza.
B. Suffis, sales&applicationdevelopment
manager - Europa, Africa e Medio
Oriente, JSP.