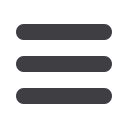
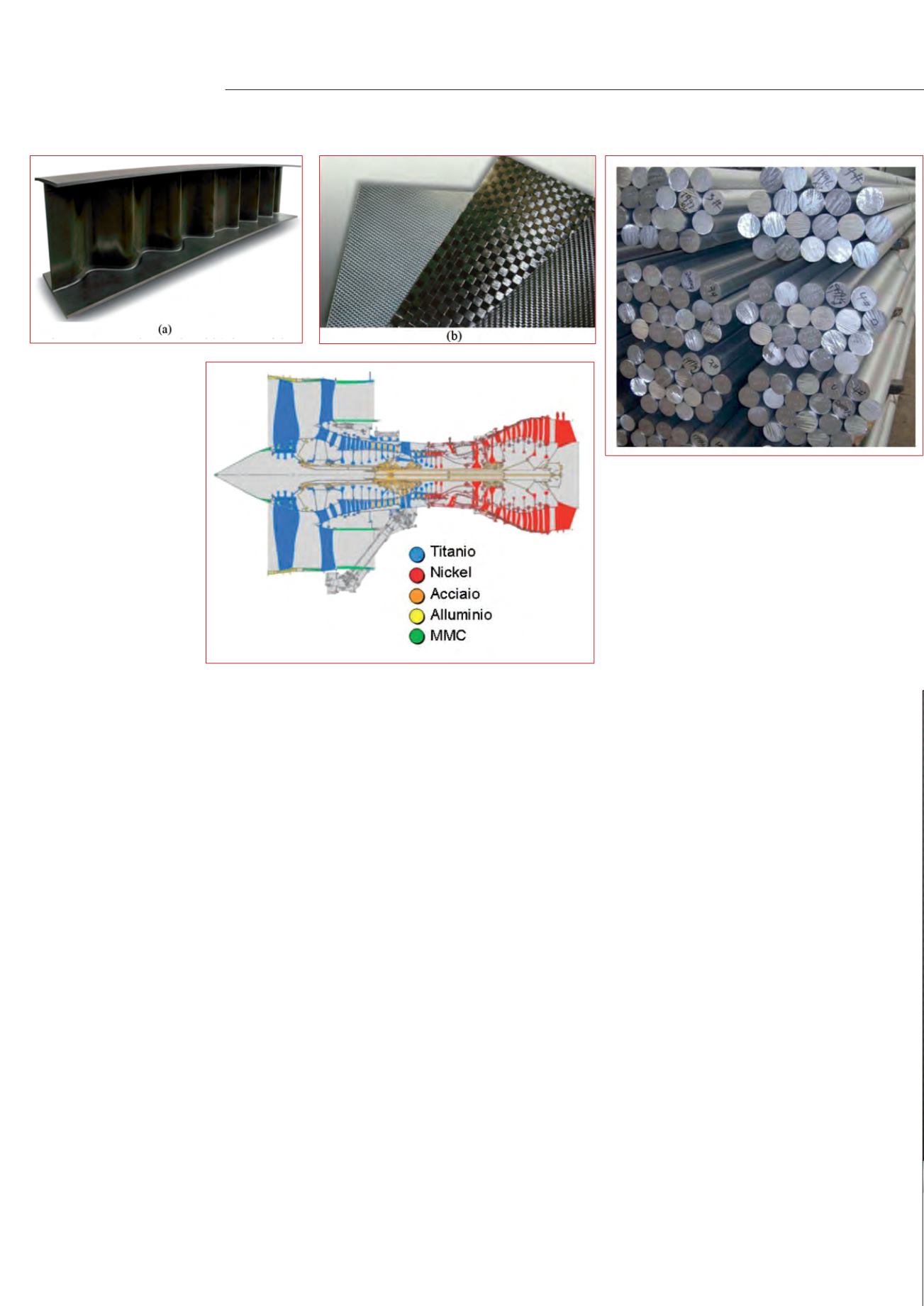
Materiali
66
progettare
392
•
settembre
2015
presenta come elementi di lega lo zinco
(Zn) ed il magnesio (Mg) e assieme al
gruppo 2XXX, sono quelle più utilizzate
in aeronautica.
Leghe di alluminio e titanio
Particolare attenzione si deve inoltre
porre alla microstruttura delle leghe di
alluminio. Per questo esse sono sem-
pre soggette a trattamento termico di
invecchiamento al fine di migliorare le
proprietà meccaniche.
Un esempio specifico di lega aeronau-
tica è la lega 7075 che tipicamente vie-
ne usata per i pannelli delle ali ed è
particolare in quanto prevede due fasi
di invecchiamento: il primo a 120 °C e
un secondo di sovra invecchiamento,
a 160-170 °C.
Questo conferisce alla lega una mag-
giore resistenza allo stress da corro-
sione. Un processo ancora migliore
per questa lega è stato sviluppato per
combinare le buone caratteristiche a
snervamento e a rottura che si otten-
gono attraverso il T6, con la buona re-
sistenza a stress da corrosione ottenuta
attraverso il T73. Recentemente leghe
alluminio-litiostannosostituendoquelle
più tradizionali in molte applicazioni
specialmente sugli elicotteri. Un altro
materiale tipicamente usato in campo
aeronautico è senz’altro il titanio e le
sue leghe. Studi su leghe di titanio con
piccole percentuali di alluminio, ferro,
molibdeno e vanadio dimostrano che
possono tranquillamente sostituire gli
acciai inossidabili austenitici fino ad
allora ampiamente utilizzati per parti
critiche di turbogetti, consentendo così
un risparmio del peso anche superiore
al 50%. Il principale vantaggio dell’uti-
lizzo del titanio rispetto a leghe ferrose
con equivalente resistenza (acciai inos-
sidabili altamente legati) è il suo basso
volume specifico.
Un albero motore forgiato in lega di
titanio (per esempio Ti 6-4 con il 6 %
di alluminio e 4 % di vanadio) risulterà
pesare la metà di un suo equivalente in
acciaio legato.
Per dare un’ idea dell’importanza odier-
na delle leghe al titanio in aviazione,
l’F-22Raptor,ilcacciatecnologicamente
più evoluto, ha un telaio formato per il
42% da leghe al titanio, per il 24% da
leghe polimeriche, dal 24% da leghe
d’alluminio e solo per il 10% da leghe
ferrose (acciai).
Infine tra i materiali convenzionali, un
discorso diverso deve essere fatto per
le superleghe a base nickel. Le superle-
ghe hanno il vantaggio di garantire una
buonaresistenzaall’ossidazioneallealte
temperature.
Lo studio delle superleghe si è svilup-
pato soprattutto in relazione al loro
utilizzo in condizioni operative partico-
larmente severe quali alte temperature,
alta resistenzameccanica del materiale,
corrosione, creepefatica. È interessante
notare, l’utilizzo di queste leghe per la
realizzazione dei principali componenti
di un motore Turbofan quali dischi,
le palette statoriche e rotoriche delle
turbine, la camera di combustione e il
compressore.
I trattamenti superficiali
Un ruolo fondamentale spetta anche ai
coating aeronautici e ai vari tipi di trat-
tamenti superficiali. Quando si parla di
Profilati di Alluminio 7075
Motore Turbofan con
materiali usati per i
vari componenti.
(a) Longherone
sinusoidale in materiale
composito (www.
premium-aerotec.com).
(b) Tessuto prepreg
(pre-impregnato con
resina) in fibra di
carbonio.