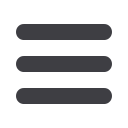
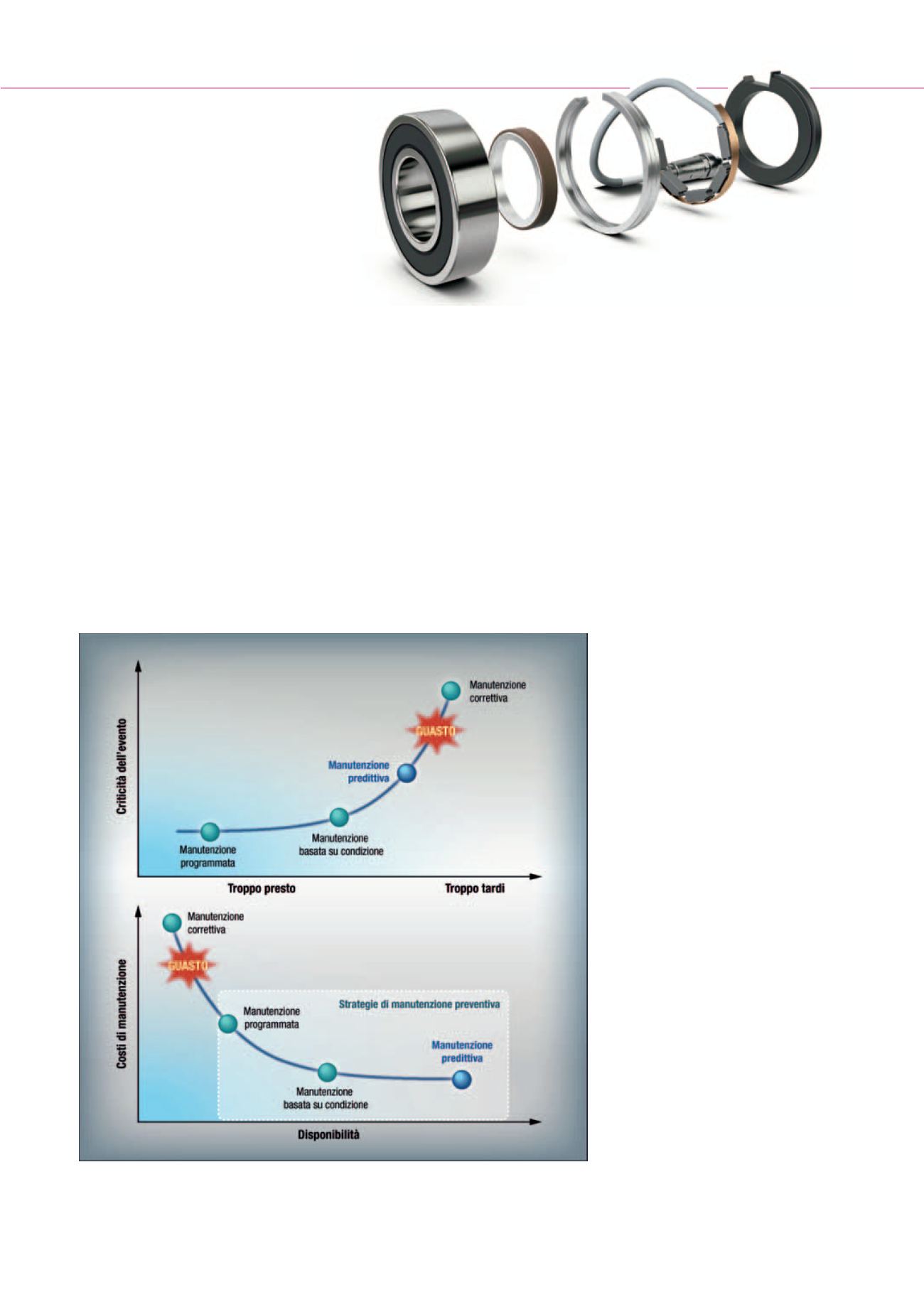
esseremisurati direttamente da senso-
ri, od ottenuti dall’operatore attraverso
opportune interface uomo-macchina,
eventualmente supportate da proce-
dure guidate. In questa fase, occorre
prestare attenzione a due aspetti fon-
damentali: i dati devono essere rac-
colti con ‘abbondanza’ e continuità,
e trasferiti verso un server (o cloud)
centrale da un’opportuna infrastruttu-
ra informatica, per essere disponibili
alla successiva elaborazione; i sensori
devono essere scelti con cura, in ter-
mini di tipologia e prestazioni, avendo
chiaro a priori a che cosa servirà la
grandezza che si andrà a monitorare.
Oggi il mercato si inserisce in questo
filone con un’offerta di componenti
pre-sensorizzati osistemi per ladiagno-
stica estremamente sofisticati, facili
da installare (plug-and-play) e a prezzi
interessanti: si pensi ad esempio ai
cuscinetti dotati di sensori in grado
di rilevare temperatura, spostamento
radialedell’alberoe/oaccelerazioni (per
esempio i VarioSense di FAG), oppure
alla svariata gamma di accelerometri
chepossonoessermontati inmandrini,
organi rotanti o componenti strutturali,
per analisi vibrometriche on-line (Mar-
poss, Montronix ecc.). È opportuno
sottolineare come molte informazioni
sono spesso già disponibili a livello
di controllo numerico, senza dover
aggiungere nuovi sensori: velocità e
posizioni di assi e motori, correnti,
assorbimenti di potenza ecc. Si tratta
solo di ricordarsene e utilizzarle.
Conversione dei dati in informazioni
Dai dati raccolti attraverso i sensori
occorre estrarre informazioni utili. Nel
corso degli anni sono stati sviluppati
diversi strumenti e metodologie pen-
sati soprattutto per la prognostica ed
applicazioni di health management
[3]. Attraverso il calcolo di indici di
integrità, vita utile residua, indicatori
di degrado, questo secondo livello
dei CPS consentirà alla macchina di
identificare il proprio stato, consen-
tendo la successiva implementazione
di strategie adattative, per esempio
adottando logiche di manutenzione
predittiva. Spesso questi strumenti
sono integrati in software multi-pur-
pose, che di volta in volta vengono cu-
stomizzati su applicazioni specifiche
(per esempio, il software Omnitrend
della Pruftechnik).
Il livello cyber coincide con il sistema
nel suo complesso, inteso come siste-
ma di produzione costituito da diversi
agenti (le macchine), che collaborano
per portare a termine la missione pro-
duttiva. Si tratta forse del concetto
più nuovo ed originale introdotto da
Industria4.0. Aquesto livello, si devono
utilizzare algoritmi di data analytics per
estrarre tutte quelle informazioni ag-
giuntivecheemergonodall’interazione
e confronto dei vari CPS tra loro. Tali
informazioni possono riguardare: un
confrontodi performance tramacchine
e/o componenti diversi, un confronto
tra i dati attuali e serie storiche me-
morizzate in un server, un monitorag-
gio del bilanciamento del consumo
energetico a livello di impianto, una
correlazione poco intuitiva tra lo stato
di degrado di un componente ed il
comportamento di un altro.
60
progettare
409
OTTOBRE
2017
Esempio di cuscinetto sensorizzato.
Il concetto di manutenzione predittiva.