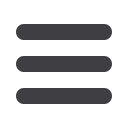
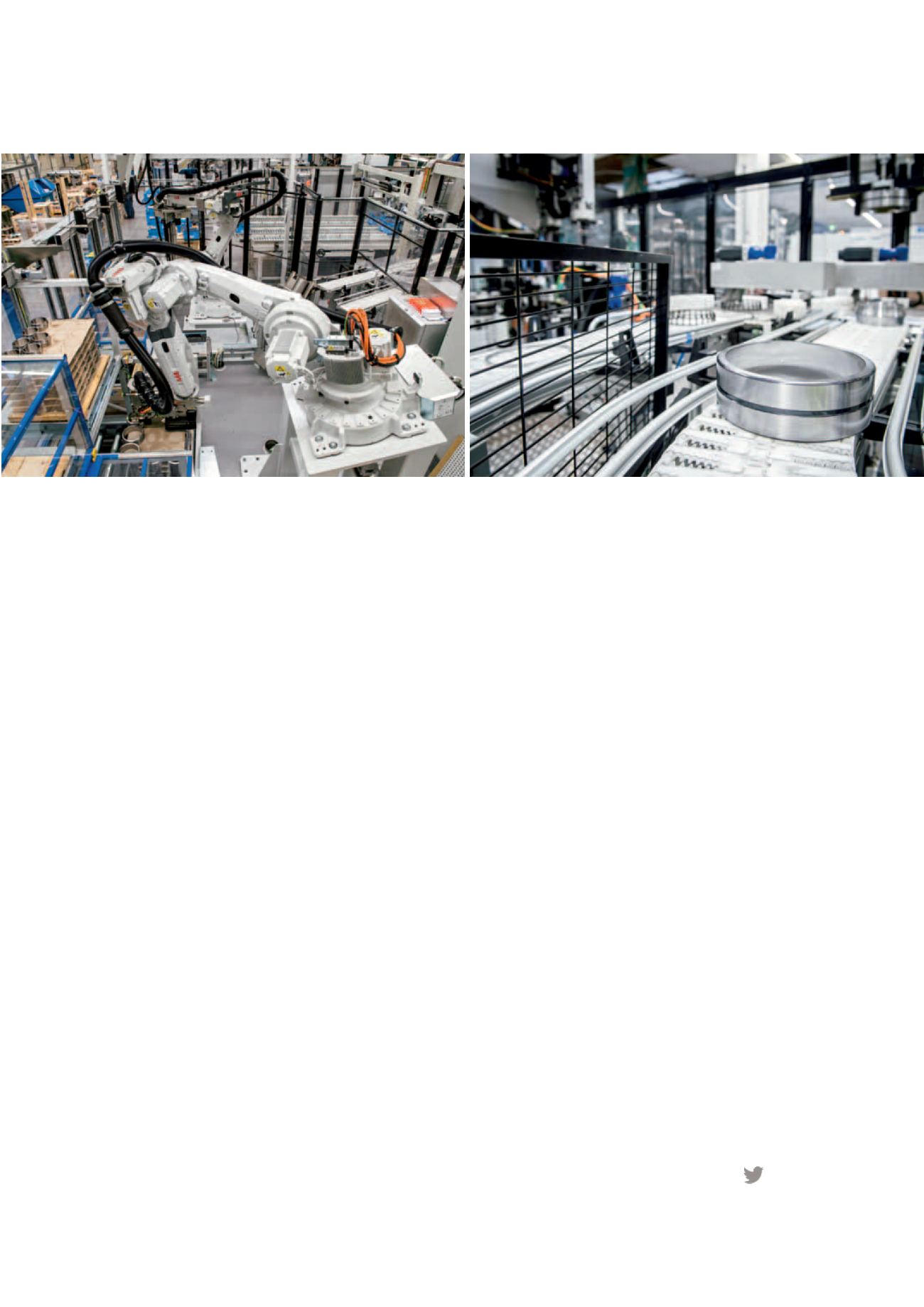
progettare
408
SETTEMBRE
2017
27
A Göteborg, in Svezia, SKF ha implementato un processo di produzione digitale completamente automatizzato e innovativo per la realizzazione
di cuscinetti orientabili a rulli.
velocità macchina e parametri di
controllo (questo attraverso una
collaborazione con Honeywell). La
combinazione di questi flussi di dati
ha aiutato uno dei nostri clienti co-
muni, un produttore leader nel set-
tore del rame, a prendere decisioni
più informate su manutenzione e
prestazioni degli asset.
Questo cliente ha confermato che il
cedimento dei componenti, che in
precedenza causava l’arresto della
produzione, ora può invece essere e-
vitato grazie alla segnalazione preco-
ce assicurata dalla combinazione dei
dati di processo e di monitoraggio”.
Abbiamo visto che l’approccio di SKF
è chiaro: l’accesso a una gamma più
ampia di dati può consentire di miglio-
rare la manutenzione e aiutare i clienti
a fare scelte più consapevoli. L’analisi
dei dati di monitoraggio e di quelli
di processo, ad esempio, potrebbe
rivelare che riducendo la velocitàmac-
china del 3% si potrebbero prolungare
gli intervalli tra interventi di manu-
tenzione di quattro settimane, dicono
i tecnici aziendali, ‘il cliente avrebbe
la facoltà quindi di compensare una
lieve riduzione della produttività con
un periodo di produzione più lungo e
prendere la decisione migliore’.
Componenti dialoganti
Veniamo ora a un’altra tematica
messa in luce da SKF: il rilevamento
automatico di cuscinetti guasti co-
stituisce un enorme passo avanti in
termini di efficienza; tuttavia, la pro-
cedura di ordinazione dei ricambi,
compresi trasmissione dell’ordine
in produzione, tempo stimato di ri-
sposta e consegna del componente,
comporta ancora un massiccio in-
tervento umano. Ebbene, l’azienda
svedese si sta già preparando per
un futuro in cui i componenti guasti
procederano efficientemente all’or-
dinazione del proprio ricambio. Da-
to che i sensori intelligenti possono
già eseguire l’auto-diagnosi, non è
difficile immaginare che possano
inviare un messaggio automatico
lungo la catena di fornitura.
Ma c’è dell’altro: la maggiore di-
gitalizzazione consente di snellire
il processo di produzione. Ha già
aiutato a ridurre i tempi di cambio
sulle macchine. In questo modo, è
possibile programmare un ricambio
specifico da integrare in produzio-
ne, riducendo al minimo i disagi e
consentendo un rapido ‘turnaround’.
La combinazione di questi due fat-
tori, previsione accurata dei gua-
sti dei componenti e ‘produzio-
ne all’ordine’, assicura che alcune
‘richieste previste’ di componenti
siano sostituite da ‘richieste effet-
tive’. In questo modo è possibile
estendere il concetto di produzione
‘just in time’ ai singoli componenti
e, in futuro, potrebbe consentire di
ridurre quasi a zero il livello delle
scorte a magazzino. “È difficile im-
maginare un mondo senza scorte,
ma questa è la prospettiva che si
profila all’orizzonte - ha concluso
van Leeuwen - questo tipo di siste-
ma deve ancora essere sviluppato.
Tuttavia, SKF sta attuando progetti
pilota in aree specifiche della cate-
na di fornitura. Il programma per
il futuro è unire questi progetti
pilota per consentire la digitaliz-
zazione totale, dall’inizio alla fine.
Ogni aspetto della catena di cre-
azione del valore in produzione
può essere migliorato attraverso la
digitalizzazione. Alcuni sono già e-
mersi, mentre altri si stanno ancora
profilando all’orizzonte. Possiamo
davvero passare dall’auto-diagnosi
all’auto-ordinazione dei cuscinetti?
Sì, possiamo: anche se per adesso
è difficile prevedere quando”.
@dapascucci