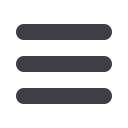
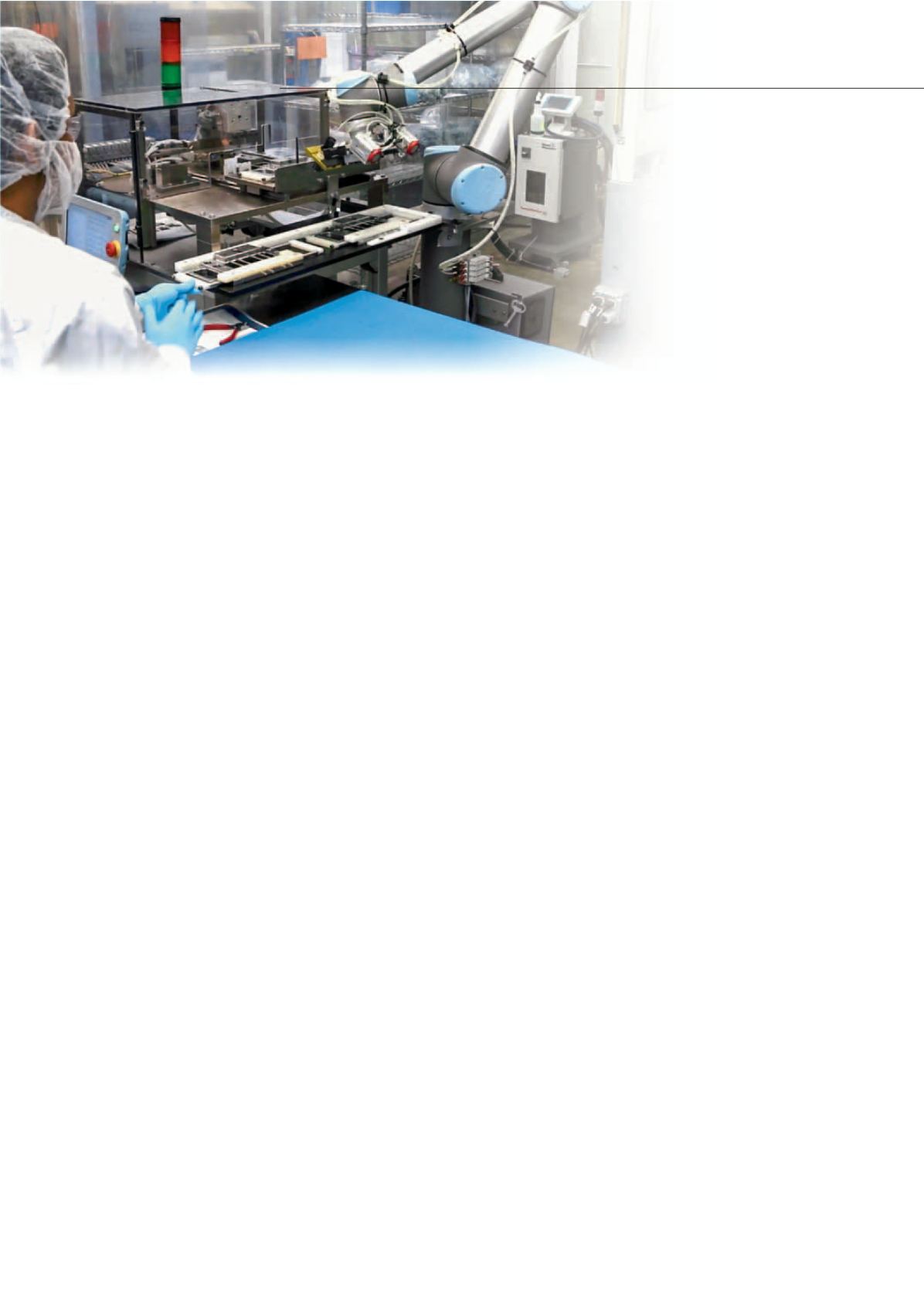
40
progettare
407
GIUGNO
/
LUGLIO
2017
Dynamic Group è un produttore ame-
ricano specializzato nella realizzazione
di stampati in plastica per il settore
medicale e nella fornitura di stampi
di alta precisione. L’azienda, nel corso
degli anni, ha maturato un’esigenza
molto netta: utilizzare al meglio la
forza lavoro applicata nei reparti per
migliorare la produttività.
La scelta conseguente è stata auto-
matizzare i processi con l’ausilio di
tre robot collaborativi Universal Ro-
bots, applicati appunto in operazioni
connesse allo stampaggio di prodotti
destinati al settore medicale. L’esito
di questo processo di robotizzazione
è sorprendente: la capacità produttiva
è aumentata del 400%.
I robot sono utilizzati in tre diverse
applicazioni. Il primo robot, un UR10,
macchina con sbraccio di 1.300 mm e
payload di 10 kg, è applicato alla pro-
duzione di un dispositivo medico con
parti molto sensibili al calore. Un pro-
cesso, quindi, che necessita di costan-
za e rigidità nei propri passaggi e nella
precisione, fattori non garantibili da
una produzione manuale interamente
L’americanaDynamic
Group, specializzata nella
realizzazione di stampati
in plastica per il settore
medicale e nella fornitura
di stampi di alta precisione,
ha introdotto con successo
all’interno dei suoi processi
tre robot collaborativi
Universal Robots,migliorando notevolmente
la produttività
Stampaggi
veloci a prova
di
errore
AUTOMAZIONE
guidata da un operatore. Per questo il
robot esegue, con precisione e costan-
za, l’intero ciclo: dal pick&place di telai
che contengono i pezzi da stampare
nella macchina fino al trasporto delle
unità a un dispositivo di taglio del
pezzo, al successivo deposito presso
una stazione di lavoro di un operatore
per concludere l’attività spingendo un
bottone che riavvia il ciclo.
Il risultato di questa applicazione è
straordinario: Dynamic Group ha ri-
dotto da 3 a 1 gli operatori applicati
a queste operazioni e ha sostanzial-
mente quadruplicato la capacità pro-
duttiva, aggiungendo un vantaggio
considerevole anche lato scarti che,
oggi, tendono allo zero. Una scelta
che, oltretutto, non ha sacrificato i
posti di lavoro: le persone impiegate in
precedenza nelle attività oggi robotiz-
zate sono passate ad altri lavori, meno
ripetitivi e più gratificanti. Il ritorno
sull’investimento, infine, è statomolto
rapido ovvero di appena due mesi.
Pezzi al sicuro
La seconda applicazione robotizzata è
relativa all’asservimento di un’isola di
stampaggio a iniezione in cui un robot
cartesiano lascia cadere su un appo-
sito scivolo il pezzo stampato. A quel
punto il robot UR preleva il pezzo e lo
posiziona su un sistema che effettua la
sbavatura e l’eliminazione delle mate-
rozze per poi poggiarlo, al termine del
ciclo, di fronte a un operatore che ne
effettua l’ispezione. In precedenza, pri-
ma dell’avvento dell’automazione, le
parti stampate potevano danneggiarsi
a causa della manipolazione dell’ope-
ratore o per accidentali cadute. Oggi,
grazie al robot, tutti i pezzi stampati
sono ‘al sicuro’ grazie alla manipola-
zione efficace della macchina UR.
Il terzo robot si occupa, infine, della
composizione di kit di prodotto. Con
l’ausilio di un gripper che effettua il
vuoto, un altro UR 10 primamovimen-
ta la parte inferiore di un contenitore
di plastica posizionandolo nella posi-
zione corretta e, a seguire, posiziona
all’interno del contenitore salviette
sterili e una soluzione salina. Infine
spinge il kit finito su un nastro traspor-
tatore. Prima della robotizzazione di
MASSIMO CAVUOTO