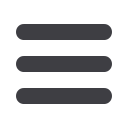
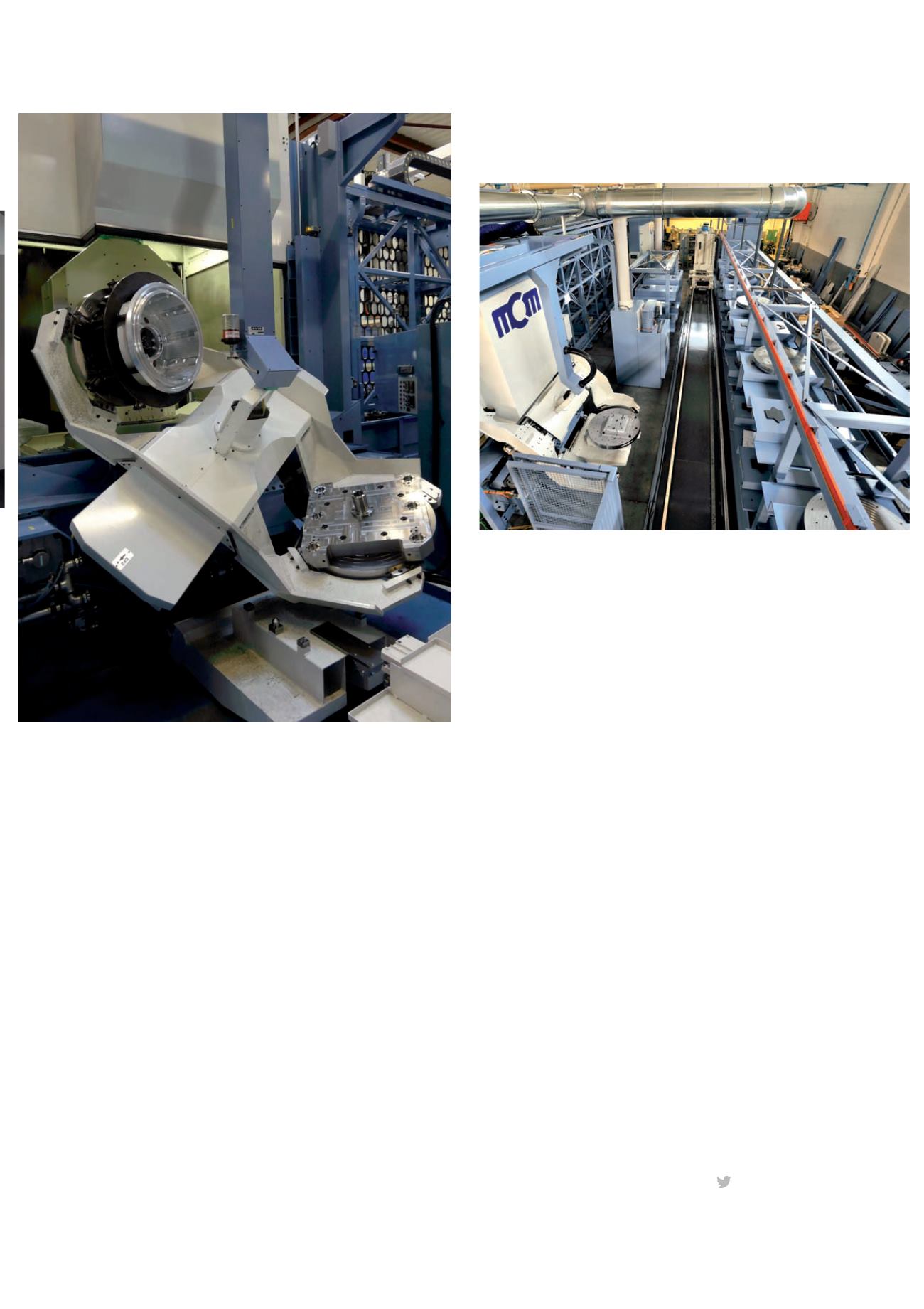
87
rmo
settembre 2015
impianto che vede presente la gamma di centri di lavoro
i.Tank 1300 multitasking ugualmente dotato di gruppo
divisore per tornitura ad asse orizzontale ma applicato
ad un altro tipo di lavorazione aeronautica. Il progetto
è stato affidato a MCM dalla società di riferimento per
la produzione di motori dei principali velivoli civili e mili-
tari sul mercato, con diverse sedi dislocate nel mondo. Il
progetto ha lo scopo di produrre parti rotanti del nuovo
motore in superlega di nickel.
Si tratta di un primo impianto FMS costituito da due
macchine, in consegna nel 2015 in Francia, con un’inte-
grazione successivadi altrequattromacchine in consegna
nel 2016, e un’ulteriore importante estensione program-
mata per il 2017. I mezzi di produzione svolgeranno ope-
razioni di tornitura, fresatura e alesatura di precisione,
contornatura e smussatura. La prima parte dell’impianto,
consegnata quest’anno, si compone di due centri di la-
voro i.Tank 130 Multitasking di fresatura e tornitura ad
asse orizzontale, dotati di gruppo divisore e di una serie
di opzioni che ne personalizzeranno notevolmente la
configurazione e le prestazioni. Gli elementi di automa-
zione abbinati alla prima parte di FMS sono dimensionati
in modo da garantire una gestione estremamente fles-
sibile della produzione prefissata. La natura modulare
delle unità produttive MCM permette una semplice in-
tegrazione delle porzioni di impianto successive e quindi
l’evoluzione programmata per gli anni successivi.
In una perfetta ottica di partnership, le analisi e gli
studi, la progettazione e le diverse esperienze, sono
stati condivisi fino al raggiungimento dell’obiettivo:
una linea di produzione unica per ruote e corone. La
combinazione delle operazioni di tornitura e fresatura
ha permesso così di ridurre il lead-time e la quantità
delle fasi di lavorazione, oltre a limitare il numero dei
mezzi necessari alla produzione. Il centro di gravità, il
momento di inerzia e la ripartizione dei pesi sono stati
aspetti fondamentali che si è dovuto tener presente
nei calcoli per il dimensionamento dei diversi compo-
nenti. I pezzi sono in leghe d’alluminio, con diametri
che vanno da 350 a 800 mm, altezze che variano da
50 a 450 mm. Le attrezzature di bloccaggio del pezzo
possono raggiungere un diametro massimo di 960 mm
per un’altezza di 570 mm.
Motore in superlega di nickel.
Anche grazie all’espe-
rienza maturata nel caso precedente, e che in MCM de-
finiscono ‘globale’ poiché è riuscita a riunire tutto il loro
know-how, l’azienda piacentina si è aggiudicata altre im-
portanti commesse. Tra queste, un esempio arriva da un
@lurossi_71
I due impianti integrati per il comparto aerospace: quello per la
produzione di route e impianti frenanti, quello dedicato alla produzione
del nuovo motore in superlega di nickel.