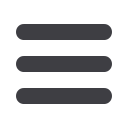
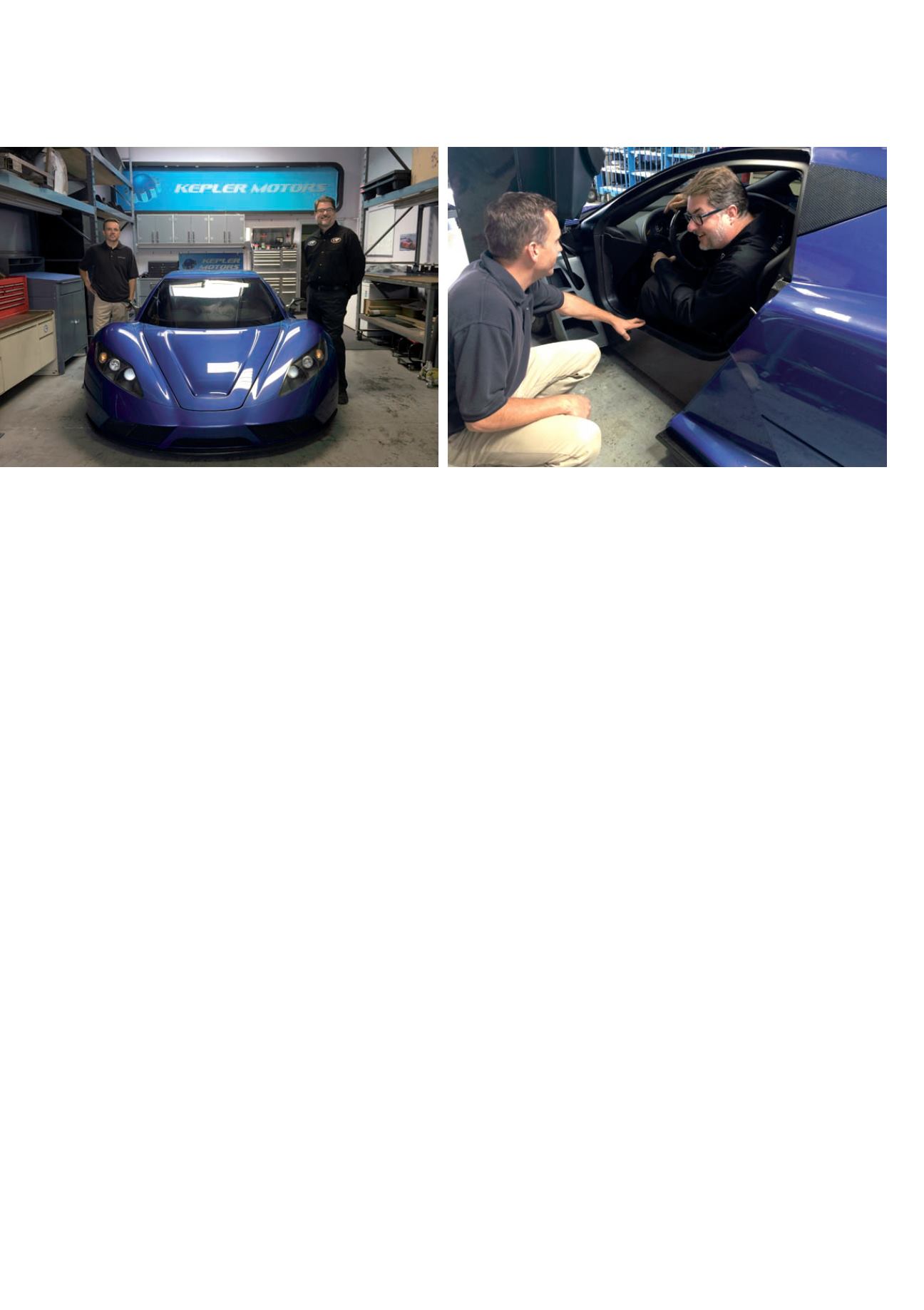
134
CENTRI DI LAVORO
rmo
settembre 2015
portato i modelli dei portamozzi realizzati con stampa 3D
alla fonderia, eseguito la fusione in titanio, effettuato la
lavorazione CNC di precisione dei componenti in titanio,
condotto l’analisi FEA e ispezionato i pezzi finali. I risultati
hanno superato le nostremigliori aspettative”.
Kepler Motors si è dunque avvalsa della competenza del
Gruppo CRP. “Abbiamo avviato questa collaborazione
con il Gruppo CRP e la sua rete di aziende perché hanno
esperienza del mondo della F1 e sanno come applicare
la fabbricazione additiva all’intero processo di progetta-
zione - ha detto Derk Hartland - sfruttare le conoscenze
di Stewart Davis e del suo team è stato un passaggio cru-
ciale nella riflessione sulla riprogettazione dei nostri por-
tamozzi” .
CRP hamaturato una grande esperienza nel mondo degli
sport motoristici, dell’industria spaziale, della difesa, del
design, dell’automobilismoedegli UAV. L’integrazione tra
applicazioni industriali e tecnologia di fabbricazione addi-
tiva, materiali avanzati, libertà progettuale e minor time-
to-market, sono alcuni dei vantaggi offerti dal Gruppo.
L’esperienzadi CRPMeccanica, CRPUSAeCRPTechnology
si estendedall’utilizzodella fabbricazioneadditiva (stampa
3D), alla lavorazioneCNCadaltaprecisione, la conduzione
di test non distruttivi durante le fasi processuali, l’esecu-
zione dei controlli dimensionali CMM volti a garantire la
completa tracciabilità di ciascunpezzo, dalla certificazione
della lega di metallo alla certificazione dei test finali prima
del montaggio sulla vettura.
“CRP Meccanica ha avuto un ruolo cruciale in tutta l’ope-
razione - ha affermato Hartland - la fusione in titano è
una ‘formad’arte’ che richiede competenza edesperienza
perché si possa giungere alla creazione di un pezzo otti-
male. Le aziende del Gruppo CRP sono state di grande
aiuto, hanno mostrato professionalità ed è stato per noi
un piacere poter lavorare con loro per l’intero progetto”.
degli elementi finiti (FEA). Insiemealla robustezza, anche il
peso è un aspetto critico per le sospensioni di qualsiasi vet-
tura. Nel caso di un veicolo come laMotion, le prestazioni
delle sospensioni hannoun’importanza vitale. Ilmontante
della Motion è stato concepito per sopportare il carico di
tutti i componenti contenendoalmassimo il peso. La com-
plessità della sua sagoma è dovuta ai diversi elementi che
devemantenere collegati.
Sinterizzazione laser.
“Leggerezza, robustezzaedurata
sono caratteristiche essenziali per far sì che la nostra iper-
car possa raggiungere le prestazioni che la caratterizzano
- ha dichiarato Russ Wicks - la fusione di titanio è quanto
di meglio la tecnologia possa offrire per questo tipo di
applicazione, una soluzione che per la Kepler Motion era
obbligata. Altre vettureutilizzano la fusioneo labillettadi
alluminio per questo tipo di applicazione, ma il risultato è
unpezzopiù ingombrante, deboleepesante. Solitamente,
quando si usa l’alluminio per i portamozzi, si aumenta lo
spessore del pezzo, riducendo in tal modo la flessibilità del
design - ha proseguitoWicks - a causa del maggiore spes-
sore del materiale, si rende necessaria una lavorazione ac-
curata capace di garantire il corretto posizionamento dei
componenti e l’ottenimento degli angoli complessi delle
facce lavorate. Ciò rende indispensabile la lavorazioneCNC
e può porre dei vincoli alla nostra creatività progettuale.
Lavorare con CRP Meccanica ci ha consentito di miglio-
rare il processo. L’impiego della loro tecnologia di fabbri-
cazione additiva tramite sinterizzazione laser, grazie alla
quale è possibile la stampa in 3D del modello da utilizzare
per la fusione del portamozzo in titanio, ci ha permesso
di concepire un pezzo forte, resistente e leggero senza
dover scendere a compromessi sul piano progettuale. CRP
Meccanica ha curato l’intero processo produttivo, dalla
progettazione al pezzo finito. I tecnici dell’azienda hanno
Coi pantaloni chiari Derk Hartland, engineering director di Kepler Motors insieme con Stewart Davis, director of
operations CRP USA.