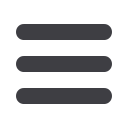
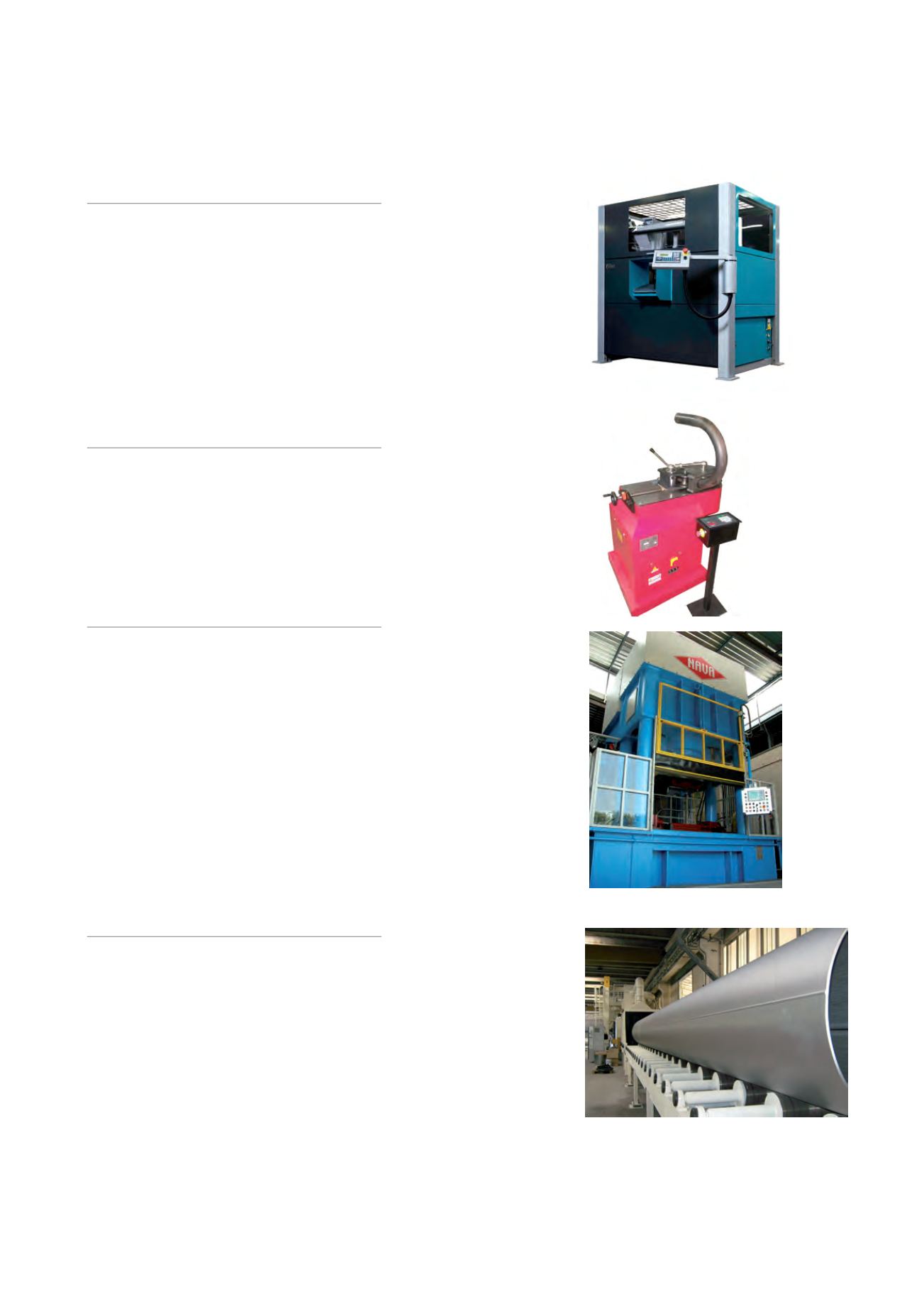
IMET
La Imet produce una segatrice automatica idraulica a nastro con struttura a montante.
Controllo di gestione a CNC per programmare varie lunghezze e quantità sulla stessa
barra. Carro avanzatore con struttura a portale e rulliera appoggia pezzo. Sistema di
avanzamento barra tramite vite a ricircolo di sfere e motore elettrico. Morsa fissa di
chiusura doppia per bloccare sia il pezzo da tagliare sia quello tagliato. Arco inclinato
di 30° per aumentare la durata della lama a nastro. Movimentazione arco su doppia
colonna e guide lineari a ricircolo di sfere. Pattino mobile movimentato tramite guida
lineare mantenuto automaticamente vicino al pezzo da tagliare. Tastatore di serie per
rilevamento automatico del punto di inizio taglio. Regolazione della pressione di chiu-
sura morse di serie. Regolazione dello sforzo di taglio di serie. Consolle di comando
mobile. Luce LED per illuminare la zona di lavoro. Totalmente ‘carterizzata’ per una
maggiore sicurezza, facile accessibilità per la manutenzione, evacuatore di trucioli di
serie. Sfrido finale di 50 mm.
MEMOLI
La nuova ETM90 della Memoli è una curvatubi robusta interamente costruita in acciaio
e con una capacità di curvare tubi di diametro massimo 90 mm e 6 mm di spessore.
Il microprocessore del pannello di controllo permette di memorizzare fino a 40 pro-
grammi, con la possibilità di cinque blocchi ciascuno. Il raggio minimo di curvatura è
2,5 volte il diametro del tubo da curvare e può variare a seconda del diametro del tubo
e del suo spessore. Peso della macchina a vuoto: circa 500 kg. Di seguito le capacità
massime. Tubo per carpenteria: 90 x 6 - 3” gas; acciaio per oleodinamica: 90 x 8 - 3”;
alluminio: 100 x 8 - 3,5”; tondo pieno (acciaio morbido): 55 - 2”; tubo quadro (acciaio
morbido): 70 x 70 x 6 - 2,5”.
F.LLI NAVA
La società F.lli Nava presenta una delle nuove applicazioni realizzate per l’idroforma-
tura di tubi. Essa si compone sostanzialmente di una pressa oleodinamica da 8.000 kN,
impiegata per la chiusura con movimento verticale della metà superiore dello stampo,
di un gruppo moltiplicatore di pressione, che produce acqua ad altissima pressione da
iniettare all’interno del tubo per farlo aderire perfettamente alla cavità dello stampo, di
due cilindri che azionano i tappi di spinta, opportunamente sagomati per fare tenuta
alle due estremità del tubo soggetto al gonfiaggio. Con tale tecnologia, implementata
con successo sia nel settore degli scarichi e delle parti strutturali per moto, sia più in
generale nei settori in cui si richiede la realizzazione di manufatti tubolari di forma
complessa e geometria variabile, è stato possibile realizzare significativi risparmi sul
costo unitario del pezzo finito, grazie a molteplici punti di forza della soluzione messa
a punto. Nello specifico degli scarichi per moto, il pezzo ottenuto ‘è vincente’ non solo
per l’ottimizzazione dei costi e l’aspetto estetico superiore, ma consente anche di ‘spre-
mere’ alcuni preziosi cavalli in più dal propulsore a parità di altre condizioni. Grazie
infatti alla assenza di saldature e allo sviluppo più fluido della geometria dei condotti, si
realizza un deflusso dei gas di combustione con minori perdite di carico.
OFFICINE MECCANICHE SAN GIORGIO
Per i manufatti metallici è fondamentale, almeno per sicurezza ed economia, scongiu-
rare gli effetti deleteri della corrosione, con opportuni trattamenti superficiali, a maggior
ragione per i tubi, spesso sottoposti a sollecitazioni meccaniche e termochimiche molto
gravose. La Omsg-Officine Meccaniche San Giorgio, specializzata nella progettazione
e produzione di macchine automatiche per granigliatura, vanta nell’ampio programma
di produzione anche un settore specifico destinato ai prodotti tubolari. Le macchine
della serie Lauco 100 H puliscono contemporaneamente la superficie interna ed esterna
dei tubi al grado Sa 3, secondo la norma ISO 8501, per mezzo della proiezione di
graniglia metallica abrasiva. Per la superficie esterna si utilizzano delle turbine centri-
fughe brevettate da Omsg, mentre per la superficie interna si agisce con lance ad aria
compressa. La graniglia viene riciclata, previa separazione delle scorie e della polvere.
Un efficiente impianto di aspirazione e trattamento della polvere forma il necessario
corredo, in ossequio alle normative vigenti in tema di ecologia e sicurezza ambientale.
Di particolare interesse è l’elevato grado di automazione, che consente una gestione
semplice dell’operazione, indipendentemente dal diametro e dalla lunghezza del tubo,
a vantaggio della sicurezza e della produttività.
rmo
aprile 2016
95