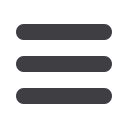
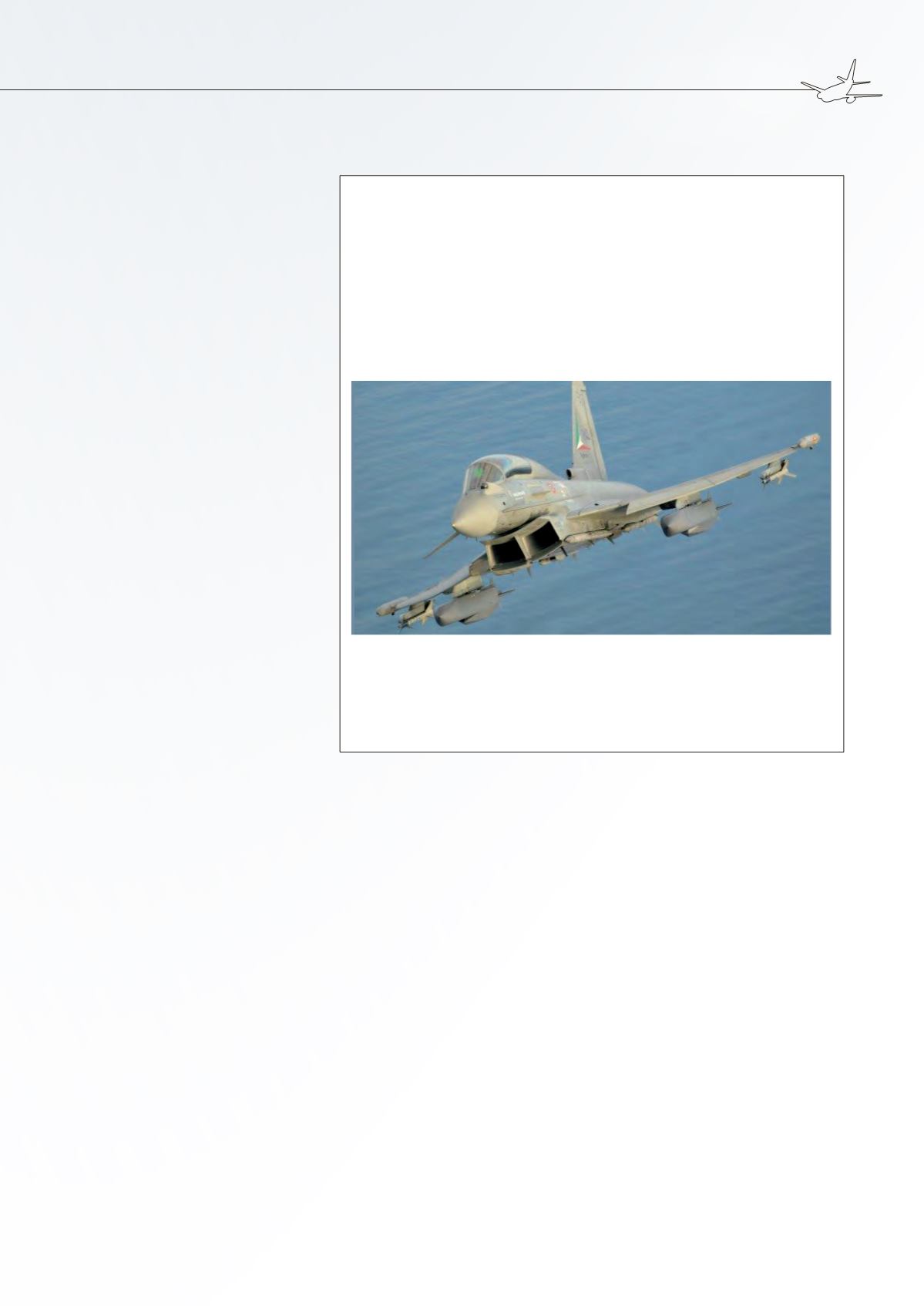
progettare
392
•
settembre
2015
73
industria aerospace
Dossier
I produttori di velivoli commerciali
sonoparticolarmente concentrati nella
ricerca di soluzioni in grado di sostitui-
re i metalli nell’ottica di ridurre il peso,
dimigliorare l’efficienza di assemblag-
gio nonché ridurre i costi operativi
e produttivi. Per tali ragioni, è fon-
damentale che i progettisti possano
accedere rapidamente a informazioni
specifiche relative alle prestazioni dei
polimeri a livello di allungamento,
temperature e altre condizioni ambien-
tali. Digimat, la principale piattaforma
dimodellazione dimateriali e strutture
multi-scala non lineari destinata alla
modellizzazione micro-meccanica di
materiali e strutture in compositi, da
oggi contiene informazioni anche su
questi tre gradi di materiali Victrex che
saranno in grado di velocizzare l’ana-
lisi strutturale e i processi di sviluppo
applicativo.
Il sistema viene considerato la piatta-
forma ottimale di modellazione per le
esigenze relative ai materiali composi-
ti di ingegneri progettisti ed utilizzatori
finali, minimizzando il peso dei com-
ponenti, i costi e il time to market. Il
polimero Victrex Peek 150CA30 viene
tipicamente utilizzato per sostituire i
metalli come l’alluminio, il titanio e
l’acciaio inossidabile. Il materiale, ca-
ricato con il 30% di fibre di carbonio,
offre elevata rigidità e forza così come
basso indice di FST (flame, smoke and
toxicity) cioè di autoestinguenza ed
emissioni di fumi e gas tossici. Poi-
ché è un materiale plastico a elevato
scorrimento, il polimero semplifica la
trasformazione sulle presse ad inie-
complesse che non sono stampabili
tramite l’utilizzo delle convenzionali
tecnologie ad iniezione.
La tecnologia Fusible-Core della Eg-
mond Plastic consente di stampare
alloggiamenti cavi complessi, collet-
tori e tubazioni. Richard Brandwijk,
managing director della Egmond
Plastic spiega: “La nostra tecnologia
Fusible-Core unitamente al polimero
Victrex Peek rinforzato con fibra di
carbonio, offre svariati vantaggi fra
i quali riduzione di costi, maggiore
velocità produttiva e, inoltre, riduzione
di peso portando a un incremento di
efficienza dei consumi e a una ridu-
zione delle emissioni di CO
2
. Oltre
al consolidamento dei componenti,
questa eccezionale combinazione fra
tecnologia emateriali consente la pro-
gettazione di particolari complessi che
va molto oltre le normali opzioni stan-
dard ottenibili con lo stampaggio ad
iniezione e le produzioni con metalli”.
Utilizzando un processo di stampag-
gio finito per il nucleo si ottiene un
risparmio di tempo dell’80% rispetto
ai componenti realizzati da lavorazione
meccanica.
È inoltre possibile eliminare i tratta-
menti secondari anti-corrosione, come
ad esempio l’anodizzazione, mentre le
tempistiche produttive possono esse-
re ridotte del 50%. Tali fattori, nell’in-
sieme, possono offrire dei risparmi di
oltre il 30% rispetto alle equivalenti
produzioni con metalli.
“L’industria aerospaziale globale di-
mostra di poter guadagnare in mi-
sura enorme sostituendo i metalli in
applicazioni chiave, in cui la Egmond
ha dimostrato di essere all’avanguar-
dia” -ha affermato Uwe Marburger,
aerospace busines - . “Chiaramente,
la nostra competenza sul Peek e sulle
soluzioni correlate ci consente l’utilizzo
di una tecnologia che implica alcune
fra le maggiori sfide della progettazio-
ne e produzione aerospaziale”.
La piattaforma di sviluppo
Dall’alluminio al Peek
In precedenza, gli utilizzatori specificavano generalmente l’alluminio per la produzione di
componenti di serbatoi carburante, ma l’utilizzo di Peek rinforzato con fibra di carbonio ha di-
mostrato migliori prestazioni di resistenza alla fatica rispetto all’alluminio, rispondendo anche
a tutti gli altri requisiti progettuali richiesti, compresa la rigidità, l’effettiva autoestinguenza
e resistenza ai fumi e gas tossici (prestazioni FST) nonché agli agenti chimici aggressivi e,
in specifico per questa applicazione aerospaziale, la resistenza ai carburanti utilizzati sui
jet e ai fluidi idraulici Skrydrol. I particolari possono variare in dimensioni fino a 30 x 30
x 40 cm e, tipicamente, il processo è implementato per produzioni fino a 2.000 pezzi. La
tecnologia Fusible-Core della Egmond è già stata utilizzata con successo con il Victrex Peek,
ad esempio in una pompa carburante impiegata da oltre vent’anni per l’Eurofighter Typhoon,
un jet militare utilizzato in diversi Paesi europei.