Chip per semiconduttori, Bosch apre a Dresda la sua prima fabbrica AIoT
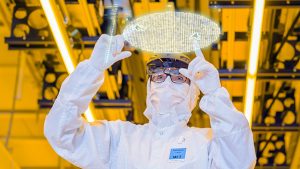
Bosch ha aperto a Dresda la sua prima fabbrica AIoT per la produzione di chip per semiconduttori completamente connessa, basata sui dati e auto ottimizzante. La presentazione della struttura high tech è avvenuta lo scorso 7 giugno, alla presenza virtuale della Cancelliera tedesca Angela Merkel, della vice presidente della Commissione europea Margrethe Vestager e del presidente della Sassonia Michael Kretschmer.
La fabbrica smart per produrre wafer impiega macchine a elevata automazione e connesse, e processi integrati combinati con metodi di intelligenza artificiale. Qui Bosch ha investito circa un miliardo di euro, il più grande investimento singolo nei 130 anni di storia della compagnia. L’inizio della produzione è avvenuto già a luglio 2021, con sei mesi di anticipo sulle previsioni, e i semiconduttori realizzati qui saranno installati negli elettroutensili Bosch. Per i clienti automotive, la produzione inizierà a settembre, anticipando i programmi di tre mesi.
In forma di microchip, i semiconduttori sono presenti praticamente in tutti i dispositivi tecnici: smartphone, televisori e wearable per il fitness. Senza i semiconduttori gli autoveicoli non potrebbero funzionare, né oggi né in futuro. Nel 2016, ogni nuovo veicolo nel mondo, aveva in media oltre nove chip Bosch a bordo, su dispositivi come la centralina elettronica degli airbag, il sistema frenante e il sistema park assist. Nel 2019 questo numero era già arrivato a più di 17, quasi raddoppiato nell’arco di pochi anni.
Negli anni a venire, gli esperti si attendono quindi un’enorme crescita dei sistemi di assistenza alla guida, di infotainment e dell’elettrificazione. Con la fabbrica di wafer a Dresda, Bosch risponderà alla crescente domanda di semiconduttori proprio in tale direzione. I componenti elettronici dotati dei chip prodotti a Dresda renderanno possibili applicazioni come la guida autonoma e la conservazione di energia, oltre che la miglior protezione possibile degli utenti. I sondaggi confermano la crescita della domanda: nel 1998, secondo ZVEI, il valore della microelettronica in un veicolo era pari a 120 euro. Nel 2018, questo valore è aumentato a 500 euro e si prevede che raggiungerà i 600 euro nel 2023.
I semiconduttori rappresentano quindi un’area di crescita anche per Bosch, e poter sviluppare e produrre in autonomia la tecnologia dei semiconduttori sarà fondamentale per l’azienda. Questi contribuiranno allo sviluppo futuro di settori come i trasporti, la produzione, l’energia pulita e l’assistenza sanitaria, ambiti di eccellenza per l’Europa, contribuendo a rafforzarne la competitività. Sono 250 le persone che già lavorano nei 72.000 mq della fabbrica, con previsione di arrivare a 700 a opere di costruzione completate.
Bosch si dedica alla microelettronica con grande impegno già dagli anni ’50, producendo in autonomia i propri semiconduttori dal 1958. Nello stabilimento di Reutlingen dal 1970 si producono componenti speciali non destinati alla commercializzazione. Da quando è stata introdotta la tecnologia di produzione per i 200 mm, nel 2010, Bosch ha investito oltre 2,5 miliardi di euro nelle sole due fabbriche di Reutlingen e Dresda. “Per Bosch, i semiconduttori sono una tecnologia fondamentale ed è strategicamente importante svilupparli e produrli autonomamente – ha dichiarato Volkmar Denner, CEO di Bosch -. A Dresda, con l’aiuto dell’intelligenza artificiale, porteremo la produzione dei semiconduttori al livello successivo: grazie alla combinazione di AI e IoT stiamo creando le basi per il miglioramento continuo della produzione basata sui dati”.
Ciò significa che tutti i dati creati, dai macchinari, ai sensori fino ai prodotti, sono raccolti in un database centrale. Ogni secondo viene così generata una mole di dati di produzione equivalente a 500 pagine di testo scritto, vale a dire l’equivalente di oltre 42 milioni di pagine in un solo giorno. I dati vengono valutati utilizzando i metodi dell’intelligenza artificiale. In questo processo, gli algoritmi di auto-ottimizzazione imparano a fare previsioni sulla base dei dati, consentendo l’analisi in tempo reale dei processi di produzione e di manutenzione. Per esempio, un algoritmo AI può rilevare fino alle più piccole anomalie nei prodotti, visibili sulla superficie del wafer come sequenze di errore specifiche, dette firme. Le loro cause vengono analizzate immediatamente e le deviazioni dal processo vengono corrette senza ritardi, ancor prima che possano compromettere l’affidabilità del prodotto.
“L’Intelligenza artificiale è un elemento fondamentale per migliorare ulteriormente i processi di produzione e la qualità dei semiconduttori, oltre che per raggiungere un elevato livello di stabilità del processo” ha dichiarato Denner. Questo comporta che che la produzione su vasta scala dei prodotti semiconduttori può essere avviata rapidamente, facendo risparmiare ai clienti automotive i tempi lunghi delle prove, che sarebbero altrimenti necessarie prima dell’avvio della produzione. Anche la manutenzione può essere ottimizzata grazie all’intelligenza artificiale. Gli algoritmi possono prevedere con precisione se un componente di un macchinario o un robot necessitano di manutenzione o di regolazione. In altre parole, queste operazioni non vengono più svolte in base a una programmazione rigida, ma con precisione, là dove serve e ben prima che si presenti qualsiasi problema.
Nella fabbrica di wafer di Dresda trova inoltre impiego il gemello digitale: nel corso della costruzione, tutte le parti della fabbrica e tutti i dati edili rilevanti correlati allo stabilimento nel suo insieme sono stati infatti registrati in forma digitale e visualizzati come modello tridimensionale. La fabbrica digitale è composta da circa mezzo milione di oggetti 3D, tra cui edifici e infrastrutture, sistemi di fornitura e smaltimento, canaline per cavi e impianti di ventilazione, macchinari e linee di produzione. Il modello digitale consente a Bosch di simulare sia i piani di ottimizzazione del processo sia il lavoro di rinnovamento senza intervenire nelle attività in corso. Anche gli interventi di manutenzione nella fabbrica di Dresda si avvalgono di high-tech: gli smart glasses con tecnologia di dati e realtà aumentata consentono di intervenire sui macchinari anche da remoto.
In altre parole, un intervento di manutenzione a Dresda può essere effettuato da un esperto di una società di ingegneria meccanica in Asia, senza che questi debba recarsi fisicamente in Germania. Grazie alla videocamera integrata negli occhiali, le immagini vengono trasmesse dall’altra parte del mondo e l’esperto in Asia può istruire e guidare passo a passo il collaboratore a Dresda, in tempo reale, lungo tutto il processo di manutenzione. Questa tecnologia ha svolto un ruolo cruciale anche per rendere possibile la messa in servizio dei macchinari nonostante le limitazioni agli spostamenti imposte dalla pandemia di Covid-19.
Contenuti correlati
-
Termocamere Flir per rilevamento di anomalie nelle pompe idrauliche
Le ultime telecamere che fanno parte della serie Exx di Flir , azienda globale nota per la ricerca e produzione di termocamere di alta qualità, sono in grado di rilevare anomalie termiche in componenti come le pompe...
-
Accordo tra Bonfiglioli Consulting ed expert.ai per introdurre l’AI nelle operations
Bonfiglioli Consulting, pioniere italiano della filosofia ‘lean thinking’ specializzato da oltre 50 anni in ottimizzazione ed efficientamento delle operations, ha siglato un accordo con expert.ai, azienda attiva nell’implementazione di soluzioni enterprise di intelligenza artificiale per creare valore...
-
Giunti elastomerici per coppie elevate ampliano la gamma Ruland
Ruland ha ampliato la sua gamma di giunti elastomerici per soddisfare i requisiti delle applicazioni con coppie elevate. Le varianti di giunti sono ora disponibili con alesaggi dei mozzi fino a 45 mm per coppie trasmissibili fino...
-
Conclusi i WorldSkills Piemonte sponsorizzati da Fanuc, ecco i vincitori per la robotica
Si sono tenuti lo scorso 23 e 24 ottobre a Torino i campionati WorldSkills Piemonte, una delle iniziative a livello regionale dei Campionati dei mestieri WorldSkills che vede la sponsorizzazione di Fanuc. L’evento ha visto protagoniste diverse...
-
Robotica e automazione per stampa 3D in metallo di grande formato con Caracol
Caracol lancia in occasione della Formnext di novembre (stand C101, padiglione 12.1) Vipra AM, piattaforma robotica integrata che mira a rivoluzionare la produzione in stampa 3D di componenti metallici di grande formato. Progettata per rispondere alle esigenze delle...
-
Serraggio rapido dei pezzi con morsa autocentrante Hoffmann Group
Nell’ottica di aumentare la produttività di industrie e piccole e medie officine meccaniche, Hoffmann Group presenta la morsa autocentrante multifunzionale Garant Xtric. Grazie allo speciale sistema di serraggio, consente di cambiare le ganasce in soli 8 secondi...
-
Schneider Electric e CNOS-FAP insieme per formazione tecnica e orientamento
La Fondazione Schneider Electric, in collaborazione con Schneider Electric Italia, e la Fondazione CNOS- FAP ETS, che coordina in Italia l’attività dei centri di formazione professionale dei Salesiani, lanciano una iniziativa della durata di cinque anni per...
-
Efficienza energetica migliorata fino a 14% nei compressori senza olio CompAir
CompAir ha ampliato la sua collaudata gamma di compressori aria rotativi a vite DX senza olio con la nuova serie DX90-160 (RS), che offre un miglioramento dell’efficienza energetica fino al 14%. La gamma è stata progettata per...
-
Digital Mentoring e talent attraction nelle PMI con Future Age
Future Age, realtà specializzata in change management e innovazione ad alto impatto per le PMI, affianca le imprese nel loro percorso evolutivo verso smart manufacturing e digitalizzazione con un team di Digital Mentor, manager con formazione ingegneristica...
-
Alberto Bassi alla presidenza del Cluster tecnologico nazionale Made in Italy
Alberto Bassi, professore ordinario di design dell’Università Iuav di Venezia, è stato eletto presidente del Cluster tecnologico nazionale MUR ‘Made in Italy’, subentrando a Matteo Tonon. Il 21 ottobre scorso si è tenuta l’Assemblea nazionale dove è...