Automated metal additive manufacturing with EOS and Premium Aerotec
-
- Tweet
- Pin It
- Condividi per email
-
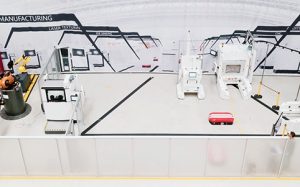
A first pilot plant has been put into operation since almost two years within the industrial NextGenAM project, a collaboration among Premium Aerotec, Daimler and EOS, aiming to enable automated metal additive manufacturing of end-use parts in the aerospace and automotive sectors.
Built at Premium Aerotec in Varel, Germany, the facility is made up of a range of 3D printing, post-processing and quality assurance technologies, and they are all fully automated and integrated. Some manual steps of conventional AM workflows have been removed entirely here, and the partners say the production of complex, lightweight and robust components can now be achieved more profitably.
The project has already succeeded in significantly reducing the production cost per part, thus creating an economic perspective for large-scale digital 3D printing factories.
At the centre of the automated AM workflow for series production is the EOS M 400-4 multi-laser system. The machine was designed for the manufacture of metal components, and in the Varel plant is equipped with a powder station and connected to a stand-alone setup and unpacking station. It allows loading and unloading, as well as preparing build jobs and unpacking built components, to be carried out independently of the build process. Transport of components between the individual stations is fully automated and protected in a gas container throughout.
Post-processing has been automated as well, using a a robot that places the full build platform into a furnace for heat treatment, and then removes it and takes it to be measured for quality assurance. Finally, the parts will be sawed from the build platform and made ready for further use.
The purpose of the project from the outset was to lay foundations for mass implementation of additive manufacturing in serial manufacturing settings. From the outset, automation was an obvious key component of achieving the project goal.
“The integration of the AM process in an automated production line is an important milestone for the broad application of our technology in series production scenarios”, commented Tobias Abeln, Chief Technical Officer, EOS. Going forward, the NextGenAM collaborators will continue to test the technology centre in Varel, with parts of the facility being audited. Production data will be gathered and analysed, to get better understandings of process timings and cost optimisation, while qualifying aluminium as a viable supported material remains a big target for the partners – up to now, titanium has been the sole material used to manufacture parts. It represents significant progress towards developing a facility that can manufacture highly complex aluminium parts in an economical AM process for the automotive and aerospace markets.
“3D printing is well on the way to establishing itself in the automotive sector as an additional manufacturing method with great versatility – says Jasmin Eichler, Head of Research Future Technologies in Daimler -. With this collaborative pre-development project, we are taking a significant step towards achieving cost-effectiveness in metal 3D printing throughout the process chain. The project lays the cornerstone for the future realisation of larger quantities in the automotive series production process – with the same reliability, functionality, longevity, and economy as for components from conventional production”.
Contenuti correlati
-
Expanded inch-to-metric range of rigid couplings from Ruland
Ruland Manufacturing is giving users access to a wider range of off-the-shelf couplings by expanding its inch-to-metric stand coupling product line with new rigid couplings. This expansion is the latest addition to the company’s inch-to-metric, standard coupling...
-
Shaft collars Ruland for medical analysis equipment
Ruland manufactures shaft collars from carefully specified raw materials with fine finishes, high holding power and precise face to bore perpendicularity, making them ideal for the demands of medical analysis equipment. Clamp style shaft collars are commonly...
-
PPC solid-carbide barrel milling cutters from Hoffman Group
Hoffmann Group has expanded its tool family for Parabolic Performance Cutting (PPC) to include a new PPC indexable insert and Garant PPC solid-carbide barrel milling cutters for high-alloy and hardened steels. The PPC process represents a further...
-
Rolling lubricants, Total acquires Houghton’s business
Total announces the acquisition of Houghton International’s aluminum hot-rolling oil (AHRO), steel cold-rolling oil (SCRO) and tinplate rolling oil (TPRO) business in the North American and European markets. The transaction also includes the associated technical support services...
-
Versatile metal tubes end-forming from BLM Group
The E-Form by BLM Group is a powerful and versatile end-forming system for metal tube ends able to carry out many integrated operations, such as deformation, end-machining, forming and rolling. It is possible to program over 9...
-
High-precision micro-milling cutters by Hoffmann Group
The Garant solid carbide micro-milling cutters by Hoffmann Group ensure high-precision machining, offering a tolerance band of just 0 to -0,005 mm, and are intended for toolmaking and mould making. The Garant micro precision milling cutters are...
-
Robotics research between Moog and IIT
Moog announces the agreement for the creation of a research Joint Laboratory with IIT, the Italian Institute of Technology in Genoa, Italy, aimed to develop quadruped robots actuation, control and power systems. During the next three years,...
Scopri le novità scelte per te x
-
Expanded inch-to-metric range of rigid couplings from Ruland
Ruland Manufacturing is giving users access to a wider range of off-the-shelf couplings by expanding its inch-to-metric...
-
Shaft collars Ruland for medical analysis equipment
Ruland manufactures shaft collars from carefully specified raw materials with fine finishes, high holding power and precise...
Economy read all ▶
-
Simulation in motorsport for Peugeot Sport hypercar with Dassault Systèmes
Dassault Systèmes and Peugeot Sport, the motorsports division of Stellantis, announced their partnership to...
-
RF rotary joints, Servotecnica signs agreement with Diamond Antenna
Servotecnica announces the agreement signed with the US company Diamond Antenna, supplier of world-class...
-
New advanced robotics hub for Universal Robots and MiR in Denmark
Universal Robots, the Danish collaborative robot (cobot) company, and Mobile Industrial Robots (MiR), the...
Technology read all ▶
-
Two-stage pressure regulator Emerson for hydrogen-powered vehicles
Emerson has introduced a new two-stage pressure-reducing regulator intended to maximise efficiency and improve...
-
High payload vertical articulated robot Mitsubishi Electric
Mitsubishi Electric has launched the Melfa RV-12CRL vertical articulated robot, which offers 1,504 mm...
-
Highly reliable pressure sensor Parker Hannifin for hydraulic applications
Parker Hannifin has introduced the SCP09 pressure sensor, a versatile and reliable solution for...