Aria compressa senza olio con i compressori CompAir
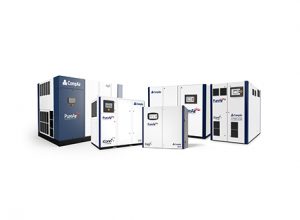
I compressori oil-free di CompAir riducono il rischio di contaminazione da olio in applicazioni igieniche, come nel farmaceutico o nei settori alimentare e delle bevande o negli ambienti sensibili in elettronica e automotive, che richiedono livelli sempre più elevati di purezza dell’aria dai loro sistemi di aria compressa.
In molti di questi processi, l’aria compressa entra in contatto diretto con i prodotti e le conseguenze possono essere gravi se l’aria è contaminata da olio o altre particelle. Di contro, come afferma David Bruchof, product manager per i compressori oil free di CompAir, parte di Ingersoll Rand, investire nelle tecnologie dei compressori oil free, come i modelli Ultima, serie D o serie DX dell’azienda, combinati con un recupero intelligente del calore, può dare presto i suoi frutti.
I vantaggi della tecnologia oil-free sono molteplici e possono aiutare i gestori dell’energia a risparmiare sui costi e a migliorare l’efficienza operativa. I costi dell’intero ciclo di vita si riducono e le aziende possono risparmiare sul costo della sostituzione dell’olio. A differenza dei sistemi lubrificati a olio, che richiedono intervalli di sostituzione dell’olio per tutta la loro durata, non è necessario acquistare apparecchiature per la pulizia e la separazione dell’olio dall’aria, come separatori d’olio, impianti di filtrazione e trattamento della condensa.
I prodotti della gamma CompAir offrono prestazioni al 100% oil-free, con opzioni a velocità fissa o regolata e modelli raffreddati ad aria e ad acqua, tra cui:
• Modelli da D15H (RS) a D37H (RS) monostadio, a iniezione d’acqua, da 37 a 75 kW
• Ultima da U75 a U160 a due stadi, raffreddati ad acqua e ad aria, da 75 a 160 kW
• Modelli bistadio da D37 (RS) a D160 (RS) da 37 a 160 kW
• Modelli bistadio da DX200 (RS) a DX255 (RS) da 200 a 355 kW
La gamma della serie D comprende in particolare modelli raffreddati ad aria e ad acqua da 37 a 75 kW ed è disponibile sia a velocità fissa sia a velocità regolata (RS), garantendo affidabilità, efficienza dinamica, costi di esercizio ridotti e aria compressa di alta qualità senza olio. Negli elementi di compressione non viene utilizzato olio, né per la tenuta o la lubrificazione dei rotori, né per raffreddare direttamente il processo di compressione, riducendo il rischio di costosi fermi macchina e di prodotti contaminati.
Il compressore CompAir Ultima è stato invece progettato con due motori a magneti permanenti ad alta efficienza che sostituiscono il tradizionale design a ingranaggi. Questi motori possono raggiungere velocità fino a 22.000 giri/min e un’efficienza superiore a IE4, ed azionano direttamente i gruppi pompanti senza la necessità di un riduttore. Mentre i modelli tradizionali lubrificati a olio utilizzano ancora l’olio per lubrificare e raffreddare i motori e i gruppi pompanti del sistema, Ultima utilizza l’acqua in un sistema a circuito chiuso. Ciò consente una maggiore efficienza di trasferimento del calore e di raffreddamento, oltre a garantire che nel sistema venga utilizzato il minor quantitativo possibile di olio per assicurare la purezza dell’aria.
Di recente è stata introdotta anche una variante raffreddata ad aria, il primo compressore oil-free raffreddato ad aria che offre il recupero del calore per l’acqua di processo. È possibile recuperare fino al 98% del calore generato durante la compressione, ottenendo un risparmio sui costi di circa 80.000 € rispetto ai modelli concorrenti più vicini.
I modelli della gamma da D37 (RS) a D160 (RS) offrono una compressione al 100% senza olio e prestazioni robuste grazie al resistente rivestimento duro dei rotori e delle parti dell’alloggiamento. Un motore IE3 o l’opzionale IE4 garantisce l’efficienza, mentre il raffreddamento ad aria contribuisce a ridurre i livelli di rumore e le perdite di pressione. Per aiutare gli operatori a ottimizzare le prestazioni energetiche, tutti i modelli sono dotati del controller touch screen Delcos XL, che fornisce una panoramica completa di tutti i parametri del compressore e le opportunità di ridurre il costo annuale di proprietà.
I modelli della gamma DX200 (RS) – DX255 (RS) sono dotati di un gruppo pompante all’avanguardia che offre un’efficienza notevolmente migliorata e una portata d’aria ai vertici della categoria. Le varianti ‘e’ premium, con le camicie del gruppo pompante raffreddate ad acqua, consentono un risparmio energetico ancora maggiore. La gamma offre una portata fino all’8% superiore rispetto agli standard industriali, con una riduzione dell’energia fino al 7% per le unità a velocità fissa e fino all’8% per i modelli a velocità regolata. I controllori della serie Xe offrono un maggiore controllo e funzionalità attraverso un’interfaccia utente intuitiva e consentono l’accesso remoto con qualsiasi browser web comune e corrente. I modelli a velocità variabile possono mettere in sequenza fino a quattro compressori senza hardware aggiuntivo per aumentare l’efficienza e stabilizzare la pressione.
Con molte aziende alle prese con ambiziosi obiettivi di sostenibilità, la scelta di una soluzione oil-free rappresenta anche la scelta più eco-consapevole, aiutando a contribuire alle credenziali verdi di una struttura. Ad esempio, il recupero del calore offre un ulteriore potenziale di risparmio e di aumento dell’efficienza. Circa il 94% dell’energia necessaria per il funzionamento di un compressore viene convertita in calore, ma utilizzando le opzioni di recupero del calore di CompAir è possibile recuperare facilmente questa energia altrimenti sprecata.
Le aziende consumano molta energia e costi per generare acqua calda di processo, riscaldare gli ambienti o preriscaldare l’acqua per la generazione di vapore. Utilizzando le opzioni di recupero del calore di CompAir, questo calore di scarto può essere riutilizzato per generare acqua calda fino a 85°C, da utilizzare ad esempio come calore di processo nelle operazioni di produzione. Grazie a un’ampia gamma di opzioni di retrofit e all’assenza di impatto sulla fornitura di aria compressa, le aziende possono spesso ammortizzare l’investimento in meno di un anno.
Contenuti correlati
-
Startup challenge in vista della SPS Italia di maggio a Parma
Dopo il successo della prima edizione, torna SPS Italia Up Challenge, competizione che si svolge a SPS Italia, la fiera dell’automazione e del digitale per l’industria in programma dal 13 al 15 maggio 2025 a Parma. Le...
-
Automazione Dymation per efficienza nella intralogistica di Interpump Hydraulics
Dymation è stata selezionata da Interpump Hydraulics, parte del Gruppo Interpump S.p.A., per la realizzazione di un sistema di automazione presso lo stabilimento di Faenza, con l’obiettivo di ottimizzare i processi per garantire una gestione integrata delle...
-
Monitoraggio energetico Schneider Electric per la sostenibilità ESG in Lati
Lati, tra i più importanti produttori di compound termoplastici tecnici, prosegue nel suo percorso di decarbonizzazione con il supporto delle tecnologie Schneider Electric, in particolare la piattaforma per il monitoraggio e gestione dell’energia EcoStruxure power monitoring expert....
-
Innovazione e sostenibilità su strada e in pista con Dallara e PTC
Creo, la soluzione CAD 3D di PTC, è l’elemento cardine attorno al quale ruotano le attività di progettazione di Dallara, marchio iconico dell’industria automobilistica sportiva ed eccellenza mondiale che, con le sue vetture, è fornitore dei campionati...
-
Mauro Bergozza nominato nuovo presidente di Assomac
Assomac, l’associazione confindustriale che rappresenta i costruttori italiani di macchine per conceria, calzature e pelletteria, ha nominato Mauro Bergozza come suo nuovo presidente. Mauro Bergozza, già vicepresidente di Assomac e CEO di Bergi S.p.A., succede nella carica...
-
Sicurezza e sostenibilità nei servizi tessili con Mewa
Oltre a garantire la continuità nella fornitura di prodotti tessili, il sistema di panni riutilizzabili Mewa si distingue per efficacia e affidabilità: le molte aziende che utilizzano questo pratico servizio ricevono da Mewa i panni puliti, li...
-
Titanio per i sistemi di fissaggio Specialinsert per soluzioni più sostenibili
Specialinsert, realtà specializzata nella produzione e commercializzazione di sistemi di fissaggio, negli ultimi sei anni ha concentrato la propria attività di R&S sull’applicazione sperimentale del titanio, valorizzandone le proprietà al fine di creare soluzioni inedite. Il metallo...
-
Automazione, sicurezza e sostenibilità nel nuovo stabilimento Landoil a Castel Maggiore
Landoil Technology, azienda del Gruppo A+B Industrial Tools Company, specializzata nella produzione e distribuzione di oli lubrorefrigeranti e lubrificanti per macchine industriali, ha inaugurato il nuovo stabilimento e centro di ricerca a Castel Maggiore, Bologna. Con un...
-
Pompe per vuoto ultracompatte a elevate prestazioni da Coval
Coval presenta la nuova serie di micro pompe per vuoto MPXS, con cui l’azienda offre una delle pompe per vuoto più compatte e intelligenti presenti sul mercato, rimanendo fedele alle tecnologie e alla qualità che caratterizzano il...
-
Suite di servizi digitali a 360 gradi per i motori e riduttori Rossi
Rossi ha introdotto Rossi 360+, area del sito web dell’azienda dedicata a una gamma di servizi digitali studiati per semplificare e migliorare l’esperienza cliente, offrendo soluzioni avanzate e immediate per utilizzatori del prodotto, distributori e OEM. Rossi...