Ergonomic cartesian arms with position monitoring system by Fiam
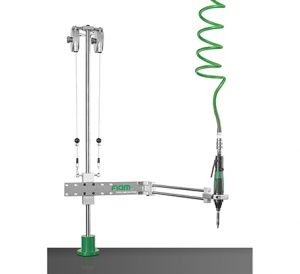
The cartesian arms designed and manufactured by Fiam are aimed to maximize ergonomics, reducing any kind of operator fatigue and ensuring the utmost safety during use, while increasing the productivity. In addition to cancelling vibrations and tool kickback on the operator’s hand, Fiam’s cartesian arms make it possible to hold the wrist in a good position and remain upright at the work station, ensuring the motion being extremely fluid and smooth.
A safety magnet holds the tool when the arm is in its rest position, and the horizontal end stops are damped with special devices. A universal clamp makes it possible to install any tool up to 50 mm in diameter. The horizontal arm can be quickly adjusted to different positions to cover a large work area.
The devices are available in two models, BC cartesian arms with simple linear travel, and BCA articulated cartesian arms, which can open in a cantilevered manner from 0 to 120° to cover large work areas very ergonomically, while retaining a small footprint.
All new Fiam’s cartesian arms can be equipped with a position monitoring device to turn them into ‘Poka Yoke’ tightening systems, which are very effective at making production cycles faster and more efficient. Such a tightening system consists of a cartesian arm complete with position monitoring device which processes either the angular movement of the cartesian arm or its angular and linear movements. A TPM (Tightening Positioning Monitor) monitoring unit stores the screwdriver positions and sequences and guides the operator through the tightening operations to ensure that the finished product is assembled in accordance with the defined specifications.
The guided positioning system operates through self-learning, by locating the screwdriver position at the various tightening points, then storing them together with the sequence of actions and the number of screws. The TPM unit display offers a graphical system to guide operators progressively as they approach the tightening point, and the screwdriver is enabled when it is at the first stored position. Each time e a screw is tightened, the display shows how many screws are left, indicating that it is ready to pass on to the next screw. A signal comes on when the stored cycle is complete, and gives the ok to proceed with a new work cycle. Finally, during the storage process, it is possible to program a precision tolerance within its operating range.